It’s hard to imagine that a mighty turbomachine like a steam or gas turbine could be crippled by something as minute as a small dent or scratch, but that reality enforces the need for regular inspection of this rotary mechanical device responsible for power generation. In particular, the bore and bolt holes found in the disk and spacer regions of the turbine rotor require close scrutiny as they are subject to high mechanical stress and are a damage mechanism target.
Various Non-Destructive Testing (NDT) methods have been employed, however Eddy Current Array (ECA) has proven to be an optimal technique when it comes to assessing turbine bolt and bore holes. Where Ultrasonic Testing (UT) suffers from what is referred to as a “dead zone” near the surface, ECA excels at detecting near-surface defects.
With purpose-built probes designed for detecting and sizing cracks, operators armed with the Eddyfi Reddy® or Ectane® ECA instruments can collect real-time C-scans quickly and accurately for reliable assessment of turbine bolt and bore holes. Packaged with the latest technology, Reddy offers the most intuitive user experience with a modern, rugged interface and a multitude of features that enable high Probability of Detection (PoD) surface inspections. Similarly, Ectane has become the undisputed reference for surface ECA worldwide. With a compact and robust form factor, the multi-technology instrument has earned a reputation for best-in-class.
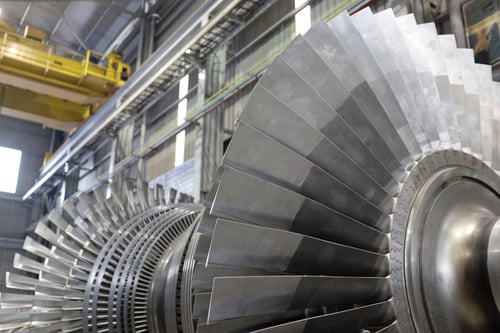
With manually operated scanners, the Eddyfi solution further performs inspections efficiently. A bore is inspected in one scan pass, while bolt holes require two quick scans. When you consider the scanning speed of our ECA probes (up to 250mm/9.8in per second!), an entire turbine bolt and bore hole is scanned almost instantly. On top of that, these probes remain sensitive to detecting cracks as small as 0.5mm/0.02in long and 0.25mm/0.01in deep.
Eddyfi Technologies’ offering of its ECA instruments and probes makes turbine bolt and borehole inspection a breeze, taking what would normally be hours of effort and condensing it to a matter of minutes. Accompanying Magnifi® data acquisition and analysis software provides powerful reporting, data management and inspection configuration operations. A common degradation mechanism also related to turbines is minute cracking in turbine dovetails, and the good news is that the same technology shines for defect detection. Learn more about inspecting turbine dovetails with eddy current array technology here.
When it comes to the surface inspection of a range of components including the bolt and bore holes on turbines, trust our Eddyfi ECA solution to deliver fast and accurate data you can rely on. Contact us to learn more about our Beyond Current advanced NDT solutions for your turbine inspections (and so much more) today.