You’ve probably already read it or heard it: corrosion under insulation (CUI) is one of the (petro)chemical processing industries worse problems, the cost associated to mitigating it astronomical.
According to the Inspectioneering, A Primer on Corrosion Under Insulation (CUI) primer report:
“In the simplest terms, corrosion under insulation (CUI) is any type of corrosion that occurs due to a moisture buildup on the external surface of insulated equipment. The buildup can be caused by one of multiple factors that are detailed below. The corrosion itself is most commonly galvanic, chloride, acidic, or alkaline corrosion. If undetected, the results of CUI can lead to the shutdown of a process unit or an entire facility, and in rare cases it may lead to a process safety incident.”
So, corrosion under insulation is one of the most difficult processes to prevent. The reason for that is, by and large, no matter the precautions taken, water invariably seeps into the insulation and begins its dirty work—sometimes unseen until process leakage occurs. Historical data shows that about 60% of pipe leaks are caused by CUI.
Temperatures Leading to Corrosion Under Insulation
It is generally accepted that carbon and low-alloy steels operating between –4ºC (25ºF) and 149ºC (300ºF) are most at risk from CUI, but aggressive CUI has also been observed in the 149ºC+ (300ºF+) range. From that perspective, preventing CUI is really a matter of making sure there’s no water in insulation systems below approximately 177ºC (350ºF) because the intermittent boiling and flashing that occurs above a metal temperature of 100ºC (212ºF) produces a fairly aggressive CUI environment.
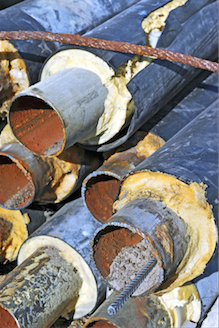
It’s difficult to predict CUI rates—they can be somewhat general in nature or highly localized. However, some of the environmental conditions leading to higher CUI rates are:
- Marine environments
- Hot or humid environments
- Climates with higher rainfall
- Steam tracing leaks
- Contaminants from the atmosphere or from the insulation (such as chlorides and sulfides) dissolving in water
- Intermittent wet-dry conditions
- Systems operating below typical atmospheric dew point (sweating services)
- Insulating materials holding moisture
- Insulation systems not allowing moisture drainage
CUI is a blanket term that refers to several different types of corrosion processes. According to the well respected article by V. Mitchell Liss of the National Board of Boiler and Pressure Vessel Inspectors, the main CUI processes are:
Galvanic
Generally results from wet insulation with an electrolyte or salt, which allows a current to flow between different metals (e.g., the insulated metal surface and the outer jacket). The extent and severity of the attack on the less noble metal depends on the difference in potential between the two metals and their relative areas.
Alkaline / Acidic
Results from moisture and an alkali or acid in certain fibrous or granular insulations. Where service temperatures exceed 121ºC (250ºF), most of the water evaporates, condenses at the edge of the insulation, and then dissolves the alkaline or acidic chemicals there, which results in corroding the jacket.
Chloride
Occurs on 300-series austenitic stainless steel surfaces when the insulation contains leachable chlorides and moisture at temperatures above 60ºC (140ºF). A concentration of chloride ions usually results from the evaporation of rain, water used in fighting fires, or process water.
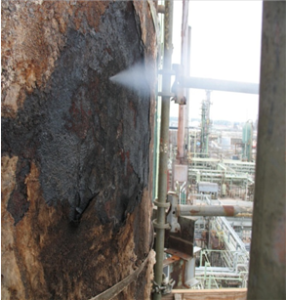
To prevent unnecessary shutdowns and accidents, the condition of equipment and piping must be monitored to detect when it should be retired from service. This is achieved in a number of ways, as it is typically more cost effective to prevent CUI than to repair or replace damaged equipment. But, equipment at plants is notoriously difficult to reach and is usually insulated, making it difficult to identify potential problems. Inspection points are selected according to where experience suggests CUI is likely to cause significant problems, but that is often not enough.
Preventing Corrosion Under Insulation
The most effective method of preventing CUI is to (of course!) keep water and electrolytes from coming into contact with the unprotected metal surface. However, it’s nearly impossible to guarantee that the insulation or coating will not be breached. Effective protective coatings and weather barriers can help minimize the potential for CUI, but effective maintenance practices will also help prevent corrosion damage before it becomes a severe problem. However, remember that maintenance alone isn’t an effective solution without a well thought out inspection strategy—none of the above mitigation practices guarantee the complete prevention of CUI.
Inspecting for Corrosion Under Insulation
Several inspection methods can help determine the presence of CUI without removing the insulation. None are foolproof and most don’t offer a good understanding of the maximum depth of the CUI damage.
- Brute force: Involves stripping the insulation off the equipment to have a look. Time-consuming, fairly expensive work process (especially if the insulation contains asbestos).
- Non-destructive testing: Allows assessing the presence of CUI without stripping the insulation. Includes various flavors of radiography (X-ray), pulsed eddy current (PEC), and UT thickness measurements from inside equipment.
- Other: Neutron backscatter and infrared thermography. Help find moisture under insulation, which may help find CUI. False calls—wet insulation, no CUI; CUI, dry insulation that was clearly very wet.
So the blight that is CUI is a complex problem to understand, predict, and mitigate. Our NDT expert, Charles Tremblay, discusses NDT methods used in mitigating CUI, outlining their pro and cons, and comparing them to each other in Corrosion Under Insulation: The 7 Inspection Methods You Must Know About.
Looking for more information? Our team would be happy to answer your specific questions related to CUI and more! Complete the form below to get in touch and stay Beyond Current with the latest product and industry knowledge directly applicable to your inspection requirements.