A large portion of bridge structures, particularly older ones and those carrying railway lines, are often constructed from steel I-beams or box section girders which are bolted or welded together. This steelwork is usually painted to help prevent corrosion (while leaving quite an aesthetic appeal – Hello Golden Gate Bridge!).
In most countries, bridge and related concrete structures are regularly inspected, at least once every two years. These inspections are mainly visual which means that only visible defects can be identified. The presence of paint or rust, together with difficult access, often present challenging scenarios making inspection very difficult or time consuming for conventional non-destructive testing (NDT) techniques.
Integrating both visual and NDT methods is essential to collect the repeatable, actionable, meaningful, and preventative data results required to effectively determine potential rehabilitation or replacement measures. Alternating Current Field Measurement, or ACFM®, is an NDT method that was developed for detecting and sizing of surface breaking defects; it is particularly well suited for fatigue cracks in and around welds on painted, coated, or corroded surfaces as there’s no need to remove the coating.
Using ACFM as an inspection method can greatly speed up inspection, reduce waste and save time compared to other NDT techniques such as magnetic particle inspection. With ACFM, you can separate the roles of a local probe operator and NDT inspector by using rope access technicians to deploy probes in hard-to-reach locations. As a result, this can avoid the need for scaffolding or other support structures, which in turn can cause closures of roads or railways under and around the bridge. ACFM provides accurate length and depth information on the size of any defect found, allowing repair efforts to be concentrated on the most serious defects, without wasting time on insignificant ones.
The TSC Amigo™ 2 is an advanced tool that truly revolutionized ACFM inspection. It offers rapid scanning using a handheld probe, provides reliable crack detection and accurate sizing—length and depth. As with all ACFM inspections, there are reduced cleaning requirements and no need to clean to bare metal. This rugged and portable instrument is designed for IP65, offering a typical battery life of 6 to 8 hours for data collection. Amigo 2 stores all data for backup, offline viewing, and audit purposes.
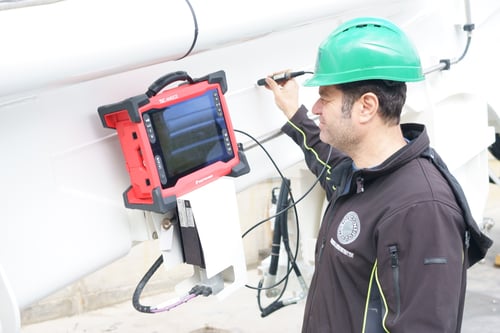
The extremely portable and lightweight counterpart to the Amigo, the TSC Pace provides ease of use with single-hand operation and has been efficiently deployed for cable stay bridge inspection.
-(Large).jpg?width=500&name=ACFM_Rotterdam-(6-of-7)-(Large).jpg)
But don’t just take our word for it. Eddyfi Technologies’ TSC product line has been directly involved in a number of bridge inspections. One of the more unusual projects involves the inspection of welds on a historic bridge, constructed in 1867, spanning the Thames river.
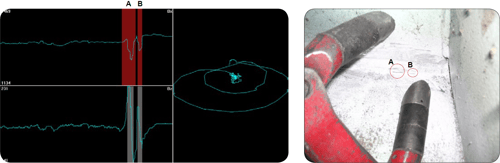
Thames Bridge built in 1867: ACFM signals from two defects on a bridge weld (left) with MPI indications from the same defects (right). Defect A was 20mm long by 3.9mm deep; defect B was 10mm long by 3.0mm deep.
Longitudinal beam web repairs had been carried out on the bridge, involving joining the original cast iron material with steel. Tests carried out on material samples prior to the inspection resulted in a high degree of confidence in ACFM for use on what is an unusual combination of welded materials, complicated by the presence of a relatively thick primer and paint coating. The Alternating Current Field Measurement technique was designed to overcome exactly these obstacles.
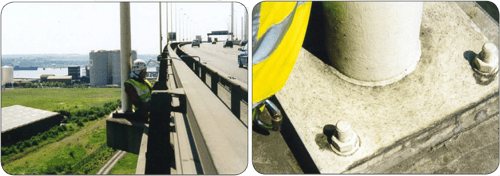
QEII Bridge (cable stayed bridge opened in 1991) ACFM inspection of lamp post welds
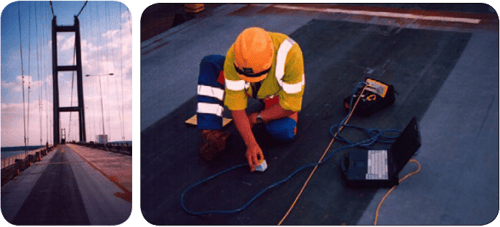
Humber Bridge (opened in 1981) deck plate inspection with Amigo kit
Eddyfi Technologies offers standard pencil probes for inspecting fillet welds. For examining other areas prone to cracking like flat surfaces adjacent to cut-outs or flat butt welds, an array probe is often beneficial. The main advantage of using an array probe over single coil probes is the much larger area that can be inspected in one pass of the probe. In addition, array probes usually include a position encoder, allowing automatic location recording and faster defect sizing.
The benefits offered by ACFM make the TSC Amigo 2 and Pace a no-brainer for more efficient bridge inspections. Gone are the days of removing paint or non-conductive coatings; save yourself a lot of time compared to conventional methods. Detection and sizing are provided from the same inspection. Rope access technicians can easily deploy ACFM technology when needed, and of course you get a complete record of all inspections for audit or review. We’d say it’s safe to say that other techniques are just water under the bridge.
Contact our ACFM experts to learn more about our advanced solutions provide real-time bridge condition information that can ultimately help extend the lifetime of this critical infrastructure.