The fourth era of industry, commonly referred to as industry 4.0, brings big changes and opportunities for the aluminum industry. It takes many forms such as the introduction of predictive maintenance. This new strategy based on data analysis brings better efficiency and cost-saving, but it hinges on the acquisition of a lot of high-quality data. This is where the Eddyfi Lyft® will give you an edge.
Industry 3.0 transformed the industrial scene with the introduction of computers and automated systems. The old assembly lines evolved to include robots which could accomplish repetitive tasks with high precision and speed. This was made possible thanks to rapid advances in technology in the fields of electronics and computer science. This advent of automation created an increased need for preventative maintenance. Scheduled maintenance was implemented to increase the reliability of assets and ensure continued productivity.
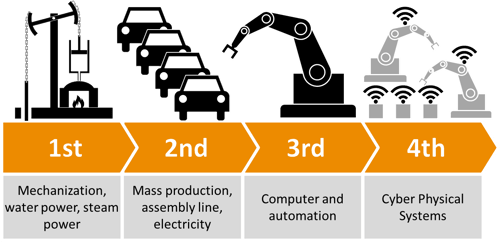
Industry 4.0 has arrived, bringing new opportunities at every level of the global supply chain. Instead of automated systems, industry 4.0 focuses on autonomous systems. Automation means that a machine continuously repeats the exact same task giving the same output every time. Newer autonomous systems analyze large streams of data from sensors to optimize their process and reach peak productivity. Gone are the days of scheduled maintenance at set and somewhat arbitrary time intervals. Predictive maintenance schedules are based on asset conditions to optimize their lifetime while also limiting costly downtime. This means the maintenance is only performed when needed. It also means you need large amounts of high-quality data to inform your decisions.
This strategy is especially well suited for the integrity management of piping. Indeed, there are thousands of meters of insulated pipes over a smelter. Most of them are insulated which makes it challenging to reliably and rapidly assess their general condition. Unfortunately, layers of insulation which tend to trap humidity close to the pipe, coupled with hot temperatures create the perfect conditions for the formation of Corrosion Under Insulation (better known as CUI). One of the biggest challenges with CUI is its inherent unpredictability. There is often no way to tell whether CUI is present by just looking at the state of the insulation.
Currently, the most common Non-Destructive Testing (NDT) techniques used to monitor corrosion are Ultrasonic Testing (UT) spot thickness checks and digital radiography. The UT spot check gives an accurate measurement on a specific point. However, the measurement needs to be made on the bare surface of the pipe, meaning that one must first remove the insulation. This crucial step can prove expensive and may necessitate a shutdown of the equipment, resulting in added costs. In other situations, the presence of asbestos makes it even more challenging to remove. Both digital radiography and UT measurement fail to provide the full picture of the asset.
To make cost effective decisions with a predictive maintenance strategy, you need to know the condition of the whole asset, not just the few spot checks positions. This is where Lyft comes to the rescue. The state-of-the-art Pulsed Eddy Current (PEC) inspection system provides a full coverage assessment of asset integrity without the need to remove insulation. PEC is an electromagnetic inspection technique that can detect wall loss on ferromagnetic structures such as carbon steel and cast iron. This includes most pipes, vessels, and storage tanks present at aluminum smelters.
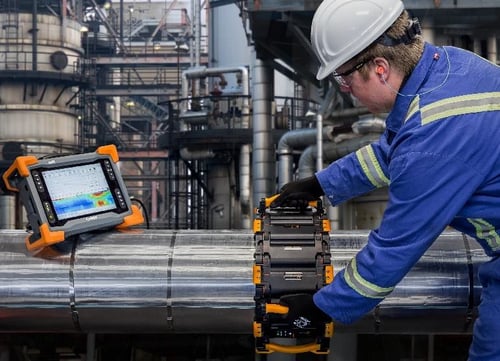
Pulsed eddy current is one of the most versatile NDT techniques on the market. It can measure the remaining thickness of a component under insulation. This insulation can take many forms such as mineral wool with an aluminum cladding or a composite wrap. PEC can also scan through thick concrete. This technique allows you to scan the asset while it is in-service without any surface preparation. Specialized accessories allow scans in contact with hot components up to 120°C (250°F).
To put the capabilities of the Lyft system into perspective, we offer an example of CUI assessment on pipes. Consider a 6-inch (168mm) pipe schedule 40 (WT: 0.280in; 7.1mm) with 2 inches (50mm) of mineral wool and 0.04 inch (1mm) of aluminum cladding. Based on typical scan speeds and acceptable efficiency, a section of 82 feet (25m) is scanned in roughly 10 minutes, excluding setup and calibration time. What brings such high productivity is Eddyfi Technologies’ unique array probe. In the previous example, the entire circumference of the pipe is scanned in just two passes with the PECA-6CH-MED probe allowing 18 inches (457mm) of coverage on a single pass. With a resolution of 3 inches by 1.5 inches the inspection gives you a total of more than 1,200 datapoints on the 82-foot section of pipe. At this liftoff and with this probe, the smallest detectable defect for a 30% wall loss defect is 3 inches in diameter. This rapid, full coverage inspection provides better insight than what a series of UT spot check through port holes ever could.
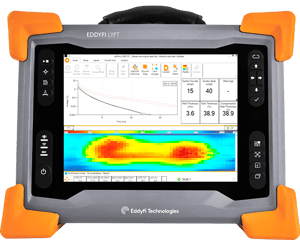
Although Lyft is particularly well suited to finding corrosion under insulation, this very versatile tool is not limited solely to this application. The same characteristics that make PEC a great fit for CUI also apply to Corrosion Under Fireproofing (CUF). The detection of corrosion on structural steel, hidden from sight beneath concrete, is a primary safety concern and a challenge perfectly suited for PEC. Lyft can also provide estimates of the remaining ligament under scab and blister corrosion. It is also a great tool to assess Flow-Accelerated Corrosion (FAC) on insulated elbows.
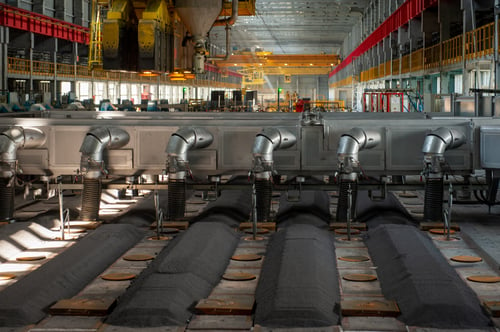
The benefits of Industry 4.0 are plentiful, but they’re only valid with the successful acquisition of repeatable, actionable, meaningful and preventative data. Eddyfi Technologies presents the Beyond Current solution that allows inspectors to work smarter, not harder, with the Eddyfi Lyft® for aluminum smelter inspection and so much more. Contact us to discuss your specific requirements today.