In order to comply with the requirements of many applicable codes and standards such as ASME and ISO, it is necessary to document the inspection parameters of the UT technique in detail. The document should include a scan plan that describes the transducer placement, motion, and component coverage to provide a standardized and repeatable methodology. Among the information required with a scan plan are the volume coverage examined for each weld, cross-sectional joint geometry including the heat-affected zone (HAZ), extent of coverage, search unit size and frequency, beam plots of all angles used, probe position and motion in relation to the weld centerline, and probe center spacing (PCS) in the case of TOFD.
Conventional UT
Conventional UT is the main ultrasonic technique for the inspection of fusion-welded joints. It has been used for quite some time and International Standards such as ISO17640 or ASME V explain the requirements necessary to define the proper procedures for weld examinations such as personnel qualification, procedure demonstration/qualification, extent of volume to be scanned, and acceptance standards.
Two important parameters to choose are the angle of incidence and the element size when performing weld examination with UT. According to Standards, one of the probe angles used shall ensure that the weld fusion faces are examined at, or as near as possible to, normal incidence. The element size shall be chosen according to the ultrasonic path to be used and the frequency. The smaller the element, the shorter the near field limit, and the larger the beam spread in the far field meaning a lower capacity to size small indications.
The following image shows a 9.5-millimeter (0.375-inch) 5-MHz conventional UT probe used to inspect a 25 millimeter (1 inch) 65° V-weld. We use two wedges: a shear 45° and a shear 60°. One can see several annotations in the 3D view: the component thickness, the index offset, the angle between the incident angle and the bevel (same side) on the second leg, the angle between the incident angle and the bevel (opposite side) on the second leg and the incident angle and the beam spread. The scan plan shows that it is barely possible to inspect the weld root using the wedge at 45°. The image on the right shows the scan plan for the SW60 wedge; we can see where the ultrasounds hit the bevel and have an idea of the focal spot size when they hit it. The angle with the bevel is 2°.
![]() |
![]() |
TOFD
TOFD is described in ASME V and ISO 10863 as an ultrasonic image generating technique, which offers the capability of detection, location, and sizing. These standards provide tables with suggested frequency, beam angle, element size, and beam intersection based on the thickness of the component. In terms of scan plan, the probes shall be set up to ensure adequate coverage and optimum conditions for the initiation and detection of diffracted signals in the area of interest.
Capture provides the following information to allow operators to carefully choose and position their probes:
- refracted angle,
- probe center space (PCS),
- beam spread,
- depth of intersection.
While TOFD has some “dead zones” due to the lateral and backwall echoes, a proper scan plan ensures maximum coverage and optimizes the chances of detecting defects close to those zones. In this example, both the toe crack and root crack are detected and sized properly.
![]() |
![]() |
For thickness ranges in steel 75 to 300 millimeters (3 to 12 inches), the beam divergence from a single element is not likely to provide sufficient intensity for good detection over the entire thickness. The examination piece shall be divided into multiple zones. The scan plan in Capture allows the visualization of multiple TOFD configurations; up to eight pairs of TOFD are possible. Based on the acceptance criterion and/or the volume to be covered, offsets can also be applied.
![]() |
![]() |
Phased Array
Phased array scanning procedures for welds shall be established using scan plans that indicate the required stand-off positions for the probe to ensure volume coverage required and appropriate beam angles. The scan plan should show the beam coverage, the weld thickness, and the weld geometry. If the evaluation of the indications is based on amplitude only, the deviation from the normal to the weld shall not exceed 6°.
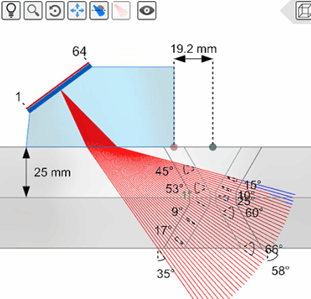
The scan plan in Capture for PAUT provides the following information:
-
Weld and HAZ overlay
-
Index offset
-
Thickness
-
Refracted angles
-
Angle between refracted angles and bevels and if it exceeds 6° from normal
-
Near field
-
Positions of first and last elements
A proper scan plan allows detection of all the indications and proper sizing using usual sizing methods such as decibel drop (for defects along the bevel) and tip diffraction.
In Capture 3.3, we introduced a new component called 2D CAD. Operators can import dxf files that can then be extruded perpendicularly to the profile (planar extrusion) or revolve along the horizontal axis (revolution extrusion).
To prepare their scan plan, operators can then select any focal laws and see the corresponding ray tracing with reflections off any surfaces going full skip or up to 20 rebounds. This is a great visual aid to verify if the ultrasounds are perpendicular to a bevel for example, to select the proper angles to reach a particular location within a component, and to select the proper area for focalization. The following image shows the scan plan for a tapered weld using a projection focusing delay law. The focus points are aligned with the bevel same side as the probe. When using focusing, focal points are moving along the rays as well as allowing for inspections to position exactly the points of focus.
Taking into account the rebound off the taper when reconstructing the S-scan allows one to reposition correctly all the indications. This also helps greatly when it comes to sizing as echoes, especially tip diffraction, are repositioned at the right locations.
TFM
The past few years have seen more and more procedures using the TFM technique. Codes state that a scan plan with a standard and repeatable methodology for examination should be provided. The scan plan shall include a depiction of the required examination volume coverage, imaging paths, image grid density, weld joint geometry, number of examination scan lines, and search unit placement and movement with respect to the weld axis. The number of pixels/pixel size is determined by following a new calibration defined in such standards as Amplitude Fidelity. ASME V and ISO 23865 state that amplitude fidelity shall be preserved to 2dB or less, and that the process applied to check this fidelity be included in the qualified procedure. Capture has implemented the experimental validation described in the ISO standard (see Code Compliant Amplitude Fidelity for TFM).
The scan plan in Capture for PAUT provides the following information:
-
Weld and HAZ overlay
-
Index offset
-
Thickness
-
Refracted angles
-
Angle between refracted angles and bevels and if it exceeds 6° from normal
-
Near field
-
Positions of first and last elements
According to ASME, direct path alone shall not be considered adequate for full volume inspection. We have defined an ROI height that takes into account the first leg and second leg. The first leg is the T-T mode and the second leg is equivalent to the indirect mode TT-TT due to the symmetry with the backwall.
For welded joints, the inspection needs to be carried out from both sides. We use two probes, one on each side of the weld, using a multigroup configuration.
Past Capture software releases have dramatically improved the possibilities to set scan plans for conventional UT, TOFD, PAUT and TFM. Operators can choose their probes, calculate their delay laws, and set their perfect standoff to ensure full coverage of their welds no matter what the UT technique is.
Stay ahead of the competition with our Beyond Current solutions, the Gekko and Panther for PWI/TFM inspections. Contact us for more information today.