It’s always interesting to hear about how someone got into NDT. Can you tell me a little about your background and how Matrix AI came to be?
Following my military service, I retrained in non-destructive testing (NDT) in 2002, working ad-hoc for a number of NDT service companies, encountering both good and bad practices along the way; this varied experience helped me learn and improve my NDT skillset. In 2007, I got my first taste of advanced NDT with phased array (PA), time-of-flight-diffraction (TOFD), and pulsed eddy current (PEC). Self-improvement has always been central to my approach and in 2009 and 2011 I completed my TOFD and phased array ultrasonic testing (PAUT) courses with TWI. Following this, I received formal PEC training with Shell Global Solutions, and I’ve been carrying out these types of inspections ever since. I’ve had the opportunity to work globally carrying out all types of inspections in and around Europe, and in Azerbaijan, Australia, and Korea.
From 2011 to 2013, I worked for a service company in Aberdeen helping to build an advanced NDT department from the ground up. This was a really good opportunity to develop my ability to establish an operation from scratch and proved to be a really enjoyable one too. At this time, I was also involved in attending meetings with Harwell Offshore Inspection Service (HOIS), the well-established joint industry project on good practices for NDT in the energy sector. I was able to take part in trials and validations, gaining more knowledge on the different equipment being used across the industry.
In 2014/2015 I was out in Korea, working directly for INPEX during the construction of a floating production, storage, and offloading (FPSO) vessel, which was designed to hold more than one million barrels of condensate. I was ultimately responsible for conducting and managing all the advanced NDT, PAUT and TOFD inspections and inspection teams working on the build. This was a really challenging but rewarding time for me and exposed me to fabrication inspections after the vast majority of my career to that point had been spent carrying out in-service inspections.
Returning from Korea, I took on the opportunity of building another advanced NDT department, but it was difficult and challenging as there wasn’t the same shared vision or willingness to fund the startup costs. This is when I started to think about forming my own company.
By 2018, I was ready to challenge myself, taking all the best practices and experience I had gained in my career to date and starting my own company focusing primarily on advanced NDT inspection services. I took a leap, selling my house to set up the business, and Matrix AI came into being in 2018. That’s the short story, anyway!
What do you think has made you successful throughout your career?
From my perspective, it’s that I come from a family background of mechanical engineers who have the shared mindset that when something is broken, we don’t just acknowledge it but also see how to fix it. Being adaptable and dynamic is very important. There’s always a plan B.

What are some things you do to keep you interested, updated, and inspired?
I’m a geek with new technology, always looking outside the NDT world to see how other technology could work for inspection. The GoPro 360 is a camera normally used for mountain biking and extreme sports. We employ it with pipe scanners to offer a 360-degree view without needing to take multiple photographs. The technology has worked so well that this option is now routinely required by most clients.
When it comes to vessels, which NDT techniques does Matrix typically use for non-intrusive inspection?
The Gekko and Mantis for PA and TOFD have really become the industry standard; we use both with the R-Scan Array. Phased array over conventional ultrasonic testing offers higher Probability of Detection (PoD) with recordable and traceable data. When a defect is found, it can easily be located with reference to a datum point using the X and Y coordinates which helps with future monitoring or repair. You also get a visual morphology of the defect, which is easy to size and show in cross section profile, aiding in the understanding of the damage mechanism, and helping to support future fitness for service assessments.
Where the vessel is heavily corroded, PA will be used, while for surface corrosion assessment, PEC with the Lyft system is used. These dual data results really give our clients increased confidence to make more accurate assessments.

You mentioned the R-Scan Array. Have you had the opportunity to use Eddyfi Technologies new LYNCS scanner?
Our recently purchased LYNCS system is scheduled for testing right now and will be deployed on a vessel inspection very soon. Both the LYNCS and new R-Scan Array are very well engineered; you can tell the thought and time that has gone into the design development and manufacture, and when you speak to the team members at Eddyfi Technologies you can hear their passion for the kit. The recent changes to the R-Scan Array with stronger magnetic wheels and breaking system are evidence they incorporate client feedback for improvement. They really went over and above to iron out some initial equipment issues and get us up and running. It is also worth noting that the support from Eddyfi Technologies as a whole has been fantastic: the loan of equipment, the Lyft technical support, and the calls with M2M have all been really good. The collaborative approach is truly an industry differentiator.
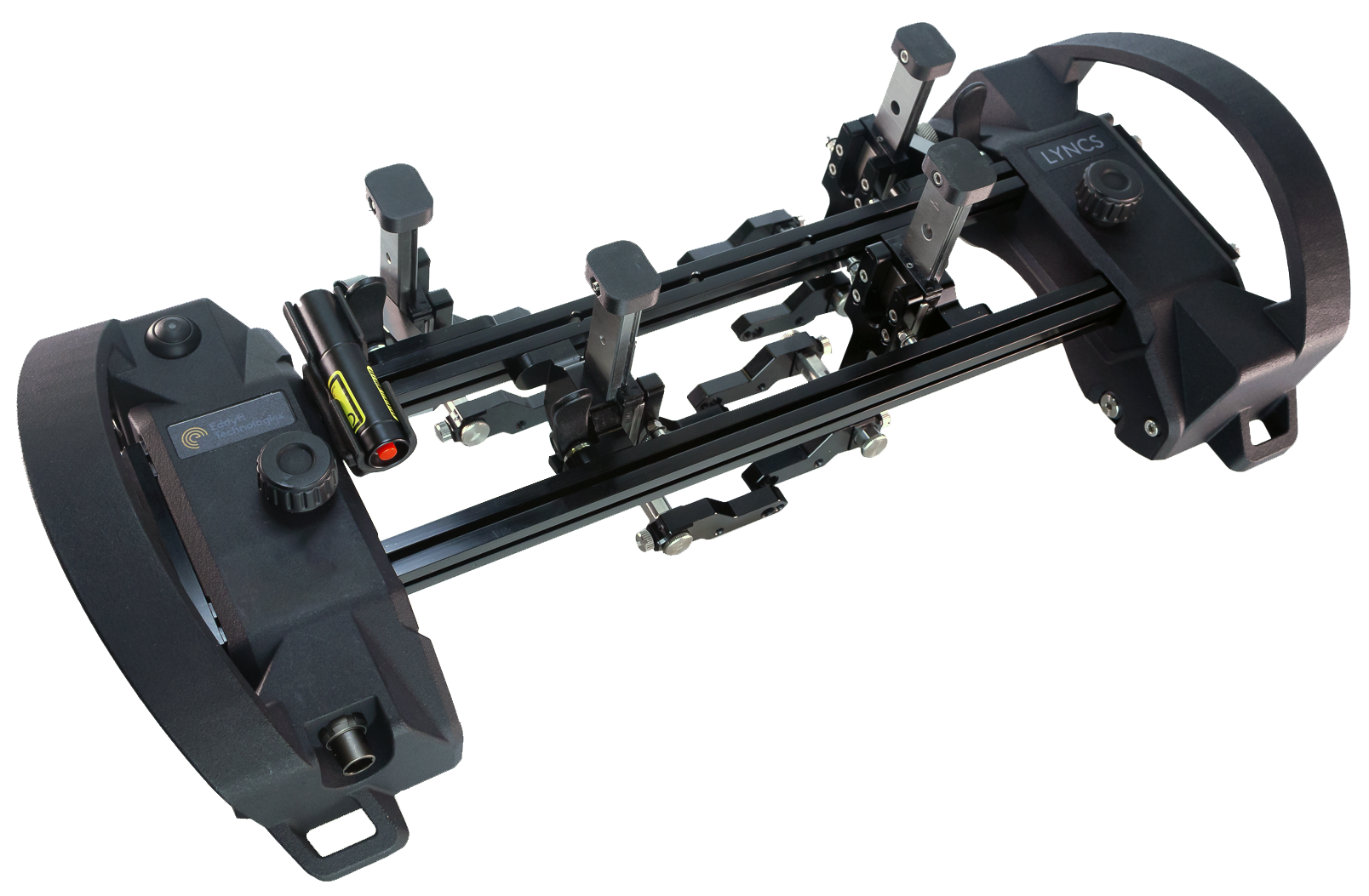
We always appreciate that feedback! Back to vessels, what are the main drivers for your customers to use NII instead of historical inspection methods?
Using the best technology for non-intrusive inspection offers clients a high degree of confidence in the results and supports their goal of trying to extend or defer the vessel inspection frequency, which can lead to substantial savings.
Do you feel that NII will eventually replace any requirements for vessel entry?
Matrix inspected 26 vessels through NII last year, minimizing manned entry with the right equipment and procedures, so that gives you a sense of the scale of the potential to avoid vessel entry. Sometimes it’s unavoidable though, like in the case of assessing internal furniture damage which is something you cannot identify using an NII approach. Most vessels normally require full internal inspections every five to ten years, but you can certainly support a deferral with NII, saving money whilst maintaining safety standards. It is a very valuable approach when it’s done right.
What do you think are some of the industry’s biggest challenges today?
There are lots of dead zones on vessels and supports where there could be potential for defects that don’t always get evaluated. Corrosion under insulation and defects in corrosion resistant alloys continue to be big challenges, trying to find cracking or pitting in clad layers in its early stages can be particularly difficult, but these are areas which Matrix excels in tackling.

When inspecting and surveying, have you ever captured anything unusual or unexpected?
One unusual example was a flare inspection where there was an issue that couldn’t be seen. There was no flame, just smoke. We regularly use UAVs inside and outside tanks and vessels for finding defects and anomalies and in this case, we added a thermal imaging camera to the drone and took another look. It turned out that the superheated flare had loosened the bolts on this 1,000-pound flare tip that was now just hanging there and could easily have fallen off. We caught it just in time!

We’ve seen a lot of sea damage. There was one steel grid escape to sea gantry that looked like it had been tied in a knot which just goes to show the power of the ocean. We do a lot of photogrammetry and surveying with drones; this is becoming part of our workflow now.
To end things off, what should our readers know about Matrix?
We are a dynamic company with a wealth of experience and knowledge in all areas of NDT in-service and fabrication inspection. We are committed to developing our team and ensuring that we deliver to the best of our abilities. We are always trying to adapt and think of new ways that we could approach the work that we do. The end goal is always about delivering a high-quality service to the end customer so that they can make informed decisions first time round.

The Matrix team is essential to our success and future growth. We foster a strong culture of inclusion and self-improvement and try to empower the team to be creative and influential in shaping the direction of the business. A big part of our appeal is down to our focus on training so that we know that whoever is out conducting inspections has the requisite skillset and competence to get the job done to a high standard.
It's quite clear that you and everyone at Matrix take great pride in your work, and it’s great to know that Eddyfi Technologies’ solutions are the tools trusted for getting the job done. Thanks for your time and industry feedback here, David!
For more information on Matrix AI, visit their website here, and if you’re ready to take the next step towards Beyond Current inspection operations, contact us today!