Eddyfi Technologies crawler tracks are small, self contained tractor modules complete with their own electric motor and drive train. They are designed for harsh environments including confined spaces, underwater, extremely hot or cold temperatures, mud and sand, mild radiation and chemical solutions. Crawler tracks drive our VersaTrax P-Series (formerly known as Versatrax 150™) pipe inspection vehicle, VersaTrax M-Series (formerly known as the MiniMag™) magnetic crawler, and VersaTrax Y-Series (formerly known as VT150 Vertical Crawler™). These patented and proven modules have also been successfully integrated in several OnSpec custom robotics.
Built on the same multi-mission modular concept as all Eddyfi Technologies equipment, crawler tracks are offered with different options to suit your specific needs. They can be fitted with an extension to increase track length. These transporter units are available in aluminum, brass or stainless steel and can have clutched or non-clutched drive wheels. In all variations, the final drive power is delivered through a deep lug rubber track belt. Crawler track units can be operated in pairs for a steerable platform (parallel vehicles) or used in multiple pairs to make a steerable train (inline vehicles). They’re available with a high voltage option. Bring us your specific inspection requirements, and we’ll offer an optimal solution.
The diagram below details the speed and loading specification for the standard crawler track. Three regions define performance:
- Continuous duty: Preferred continuous operating range.
- Short term operation: Operation permitted for several minutes.
- Stalled/jammed condition: Automatic limited is engaged to protect the motor and gearing. Do not operate the track under this condition.
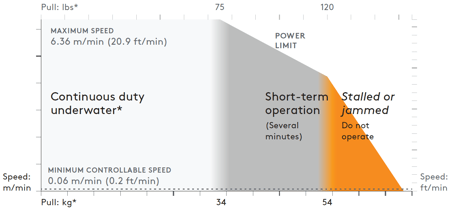
For a typical tracked vehicle, multiple factors may increase load and impact crawler track performance. Additional payload may be added to a track, but the expected pull performance must be de-rated according to the following calculation.
Additional payload also affects differential steering, inclines, and curved pipe geometry.
Inclines force crawler tracks to lift the vehicle weight against gravity and increase the track pulling load. Magnetic downforce does not affect loading from inclines, only forces from gravity. The constant load from gravity becomes a pertinent factor on vertical planes because the track motor must work to resist the load even when the track is stopped. You can calculate the incline load using the following equation.
Extra Pull = (Total Vehicle Weight) x SIN (Ø)
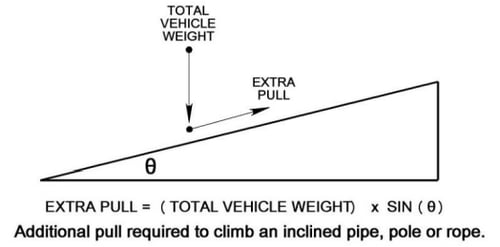
Differential steering refers to the varying speed of two tracks like that of a tank or bulldozer. During the steering process, the tracks are dragged sideways in addition to forward and backward. The sideways movement increases the total track load and therefore requires extra torque from the motor. A typical VersaTrax P-Series weighing 41 kilograms (90 pounds) on a surface with friction coefficient µ = 0.5 will experience an extra 12kg (27lb) load per track during a spot turn. The same maneuver on fine, dry concrete or low-pile carpet results in over 23kg (50lb) of extra motor load!
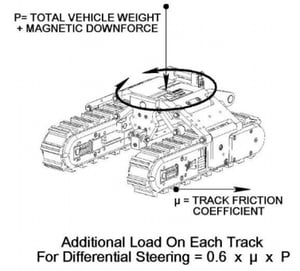
When strictly steering on a vertical surface, only include the magnetic downforce for this calculation.
Curved geometry inside a pipe will increase track payload depending on the angle of contact with the pipe. For nearly flat tracks, the increase is minimal. A contact angle of 60 degrees will double the load. The same calculation is applied for tracks contacting pipes exteriors.
Load Per Track = P / (2 x COS Ø)
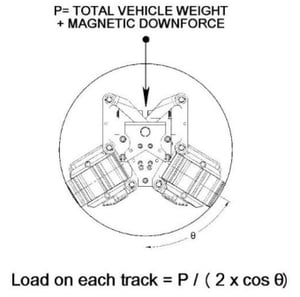
Include the vehicle weight and magnetic downforce for this calculation.
Duty cycle is the length of time a track can run before overheating. The duty cycle for a crawler track depends on:
- Track material thermal conductivity (aluminum, brass = good, stainless = poor)
- Ambient temperature
- Track load and speed
- Wet or dry operation
- Heat sinking
A crawler track typically converts about 25% of the electrical input into motive mechanical power with the remainder being converted into waste heat transferred to the environment outside the track. Normal usage will include much starting and stopping for visual/NDT inspections and moderate loading for most of a pipe run for pulling tether, so reaching the track’s thermal limit isn’t common. When tracks are bolted to a chassis, it also acts as a heat sink to keep tracks cool. If tracks are operating underwater, like in a flooded pipe, heat transfer is excellent, and the duty cycle is continuous.
So, how much weight can crawler track pull? Eddyfi Technologies’ decided to perform a test using their Chevrolet Express 1500 cargo van put in neutral with a driver to assist with steering. Don’t try this at home, kids! A robotic platform featuring two standard crawler tracks was tethered to the front of the van with three volunteers standing on it to provide extra traction. Powered by ICON™ software and driven with an Xbox controller, the crawler tracks successfully pulled this load through a gradually inclined parking lot without breaking a sweat. So what's the conclusion on weight? It depends. Our mighty crawler tracks can pull your weight!
When the inspection job calls for assessment in confined spaces, hazardous environments or generally anywhere people really shouldn’t be, Eddyfi Technologies’ robotic crawlers are designed to perform Remote Visual Inspection (RVI) and transport your sensors and tooling for your specific remotely operated operations. Like your friend with the truck, we’ll help you move! Contact us today to learn more about an multi-mission modular robotic solution.