When it comes to ensuring a safe and comfortable environment for occupants of commercial, industrial or large-scale service buildings, optimal performance of air conditioning heat exchangers is critical. Chillers are often composed of copper tubes or similar alloys responsible for transferring heat between the building’s ambient air and outside air with a fluid compression/ decompression cycle. In order to ensure efficient system performance and reduce risk of failure, exchanger tubes must be regularly inspected.
Air conditioning (AC) heat exchanger tubes present many challenges for inspectors including their variable geometry. They may have an internal or external texture or fins that decrease the space available for the probe and potentially interferes with the signal. Support zones without fins at an expanded diameter known as land areas add a change to the heat exchanger tube geometry. On top of that, access to the tubes themselves can be difficult as the chiller may be situated in a small or otherwise confined environment.
Without the right probe, your non-destructive testing (NDT) system is incomplete. While we offer fixed or detachable bobbin probes that deploy eddy currents for non-ferromagnetic tube inspection, their excellent performance detecting volumetric defects doesn’t directly apply to AC tube land areas or specific challenging defects. The reason is that these probes generate eddy currents parallel to the circumference of the tube, and the presence of cracks prone in heat exchanger tubes don’t disturb the eddy currents enough for a high probability of detection.
That’s why Eddyfi Technologies developed a family of probes powered by a portable instrument adapted specifically for the inspection of air conditioner tubes, Reddy® AC-E. To overcome the challenge of fluctuating tube diameters with or without the presence of fins, the AC probe family is offered in a range of sizes and available in diameters from 11 to 23mm per jump of 0.2mm. Often, only the outer diameter of the tubes is known and the thickness of the given wall, under certain conditions called “root”, may or may not take into account the presence of internal and/or external fins. Therefore, it is the actual inner diameter of the tube that determines the diameter of the probe to be used.
The appropriate size required is determined by the internal tube diameter. In order to occupy a maximum portion of the inner surface of the tube while leaving enough space to avoid jamming, we recommend an 88% fill factor. We also advise maintaining a 0.3mm to 1mm lift-off around the probe. The following formula can assist with calculating your optimal probe size.

To complement the true portability of the Reddy® AC-E, we’ve made our probes detachable alleviating the need to transport several probes for the different heat exchanger tube diameters often faced. Armed with an assortment of probe heads and a detachable cable, inspectors will appreciate the strong connector designed and tested for field operations, and the robust laser welded sleeve for sensor protection. The probe, connection, and cable are watertight as small amounts of water or fluid are common in AC tubes during inspection. Keeping the requirements of AC exchanger inspection in mind, we offer these probes with specific flexible polys made of HDPE or LLDPE for even the most restricted spaces requiring access. These cables feature two conventional 4-pin connectors as expected for such probes.
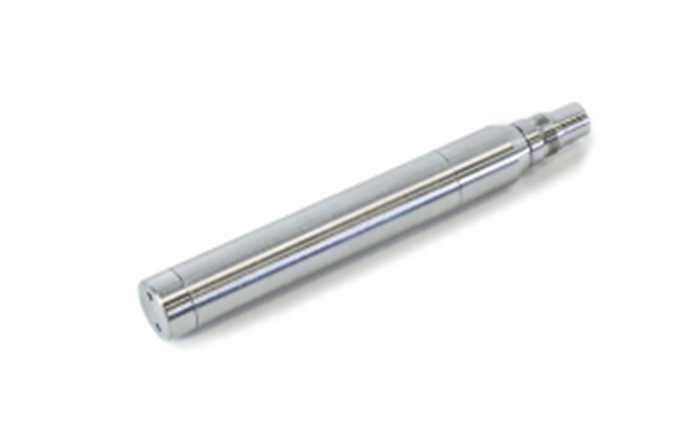
While quality mechanical design is paramount, an NDT system is only as good as the results it can report. Eddyfi Technologies’ AC tube probes includes bobbin sensors specially adapted to reduce signal noise caused by fins. The image below demonstrates the results obtained on the simulated 20% groove defect in an AC copper tube with fins. Note the presence of an absolute channel for detection of volumetric losses and the differential channel for pitting.
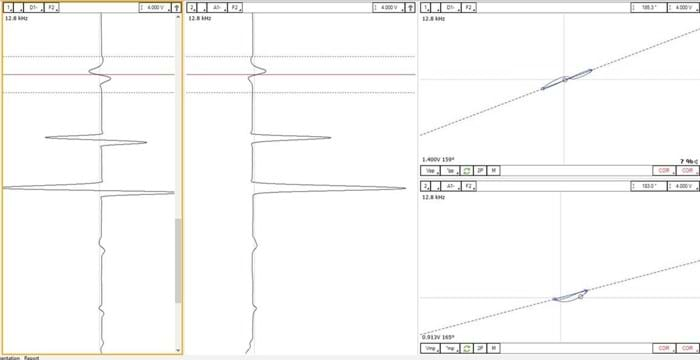
This adaptation alone doesn’t reliably detect circumferential cracks. That’s why we added specific combined probe sensors to create an “AC” data channel that can detect circumferential cracks, axial cracks, and/or non-directional defects like pits. The data below was recorded from a straight copper tube with fins and enables comparison of detection of a circumferential crack at the end of the land area with both bobbin and AC sensors. The image on the left is taken with a traditional absolute bobbin sensor and only shows the land area signal. On the right, the detection of the same crack is performed with the AC sensors – a clear advantage.
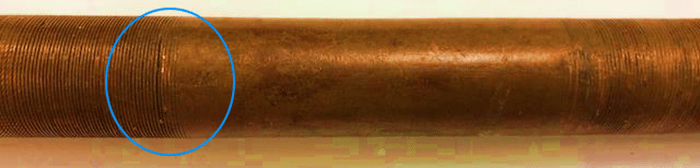
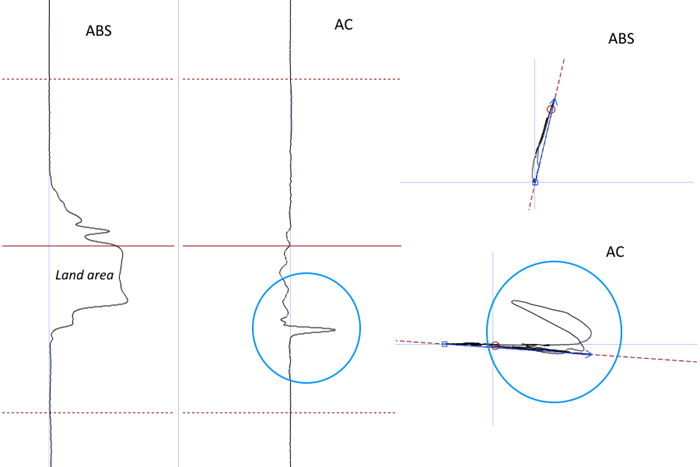
Signal disturbance caused by geometric variations on more than 90 degrees around the tube, like land area diameter changes, has been reduced with the combined AC sensors. Less disruption improves the signal-to-noise (SNR) ratio of defects found in this zone. The following image shows the difference between the signal of a diameter deviation from a conventional coil probe (differential and absolute on the left) and on the AC channel of Eddyfi probes (on the right). The effected signal in the land area is significantly larger on the bobbin signals -especially on the absolute channel - than on the AC channel, allowing the latter a much clearer signal and improved SNR for defects.
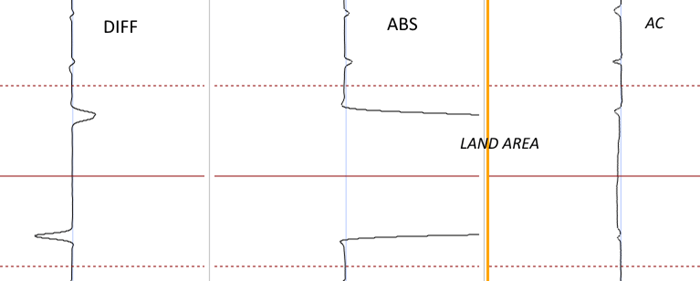
The final image demonstrates another advantage of the AC channel from combined sensors: complete coverage of the tube surface without sensitivity “holes”. The sensitivity area of each sensor covers that of its neighbor to ensure defect detection regardless the angular extension. The image shows a point signal first detected by a sensor of the AC channel, then by both this sensor and the neighbouring sensor, and then by the neighbouring sensor alone. Unlike with other probe types, there is no “dead zone” detection when you perform chiller tube inspection with Eddyfi Technologies’ AC probes and Reddy® AC-E instrument. Learn more about our BBAC probe here.
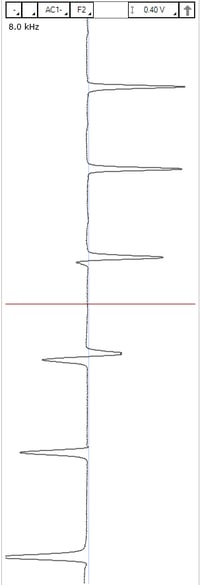
Whatever way you look, we’ve got you covered with the Reddy® AC-E and unique AC probes for the challenges of air conditioning heat exchanger tube inspections. Bringing innovation to the market, Eddyfi Technologies allows inspectors to be Beyond Current and inspect AC tubes with modern age technology. Contact our friendly and knowledgeable staff to learn about improved productivity and profitability with faster inspections today!
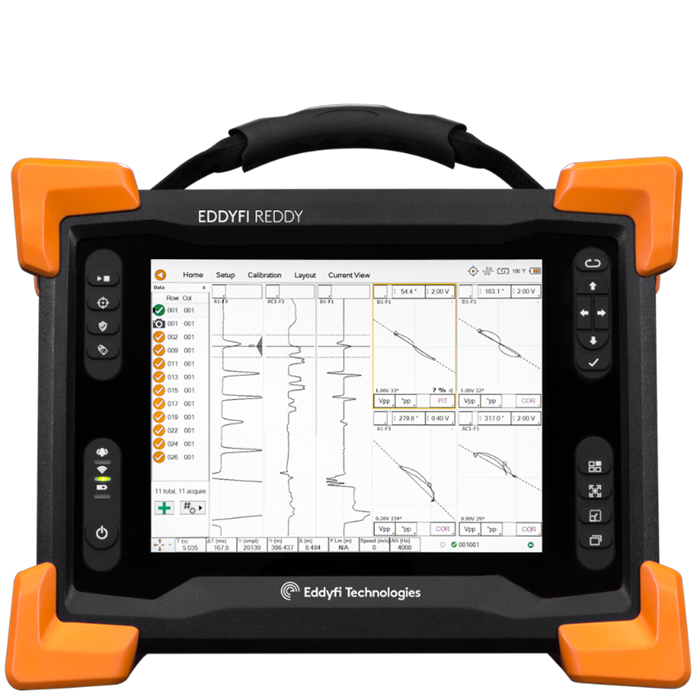