A wind turbine will undergo a range of inspections throughout its entire useful life: from the quality assurance inspection at production and installation, planned preventative maintenance scheduled over the typical five to 10-year warranty period, end-of-warranty inspection for maintenance, repair, and overhaul of new components and structure; all the way to non-routine occasional extension of lifetime assessments based on condition monitoring reports.
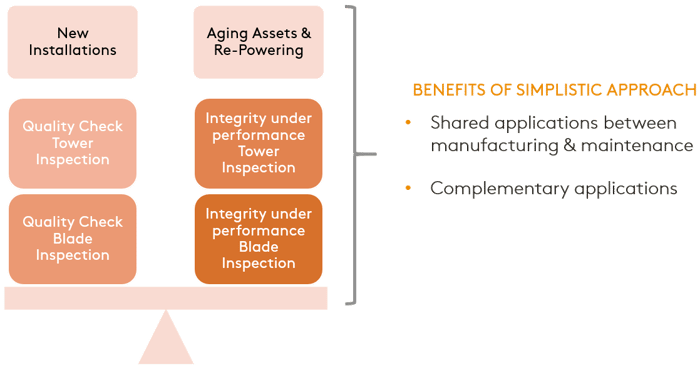
From beginning to end, the VersaTrax™ M-Series miniature magnetic crawler is a proven constant that can be found performing internal and external remote visual inspection (RVI) of wind turbine towers and blades worldwide. The versatile inspection robot features a 360° continuous tilt camera that can operate in air and underwater in otherwise inaccessible industrial environments. Delivering 1080p resolution real-time video footage, the VersaTrax operates on a user-friendly software platform leveraging the variable intensity spot and flood lights and parallel laser lines to collect the precise data required for a comprehensive, comparable inspection report; visit our eStore for more information and pricing.
The robotic deployment of Eddyfi Technologies’ NDT sensors enables an all-in-one solution for deeper analysis. For example, phased array ultrasonic testing (PAUT) can be performed on composite blades with Eddyfi Technologies range of semi-automated scanners: NDT Sweeper, NDT Paintbrush & LYNCS™; download our eBook on robotics for NDT data collection or visit our Eddyfi Academy to take a closer look. The Sharck™ probe can be used to inspect carbon steel welds for surface-breaking cracks. Our robotic crawlers can access the T-joint construction welds found on offshore wind installations for assessment by total focusing method, or TFM, with the Gekko®. Subsea, Eddyfi inspection crawlers have had great success mobilizing alternating current field measurement, or ACFM®, devices for structural weld inspections.
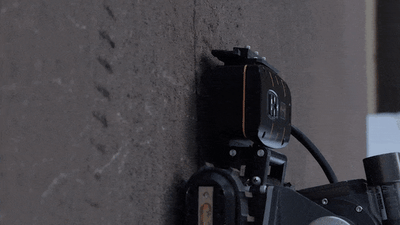
Beyond NDT, we have developed an OnSpec custom solution to fill composite holes with epoxy robotically instead of sending humans into the turbine blade.
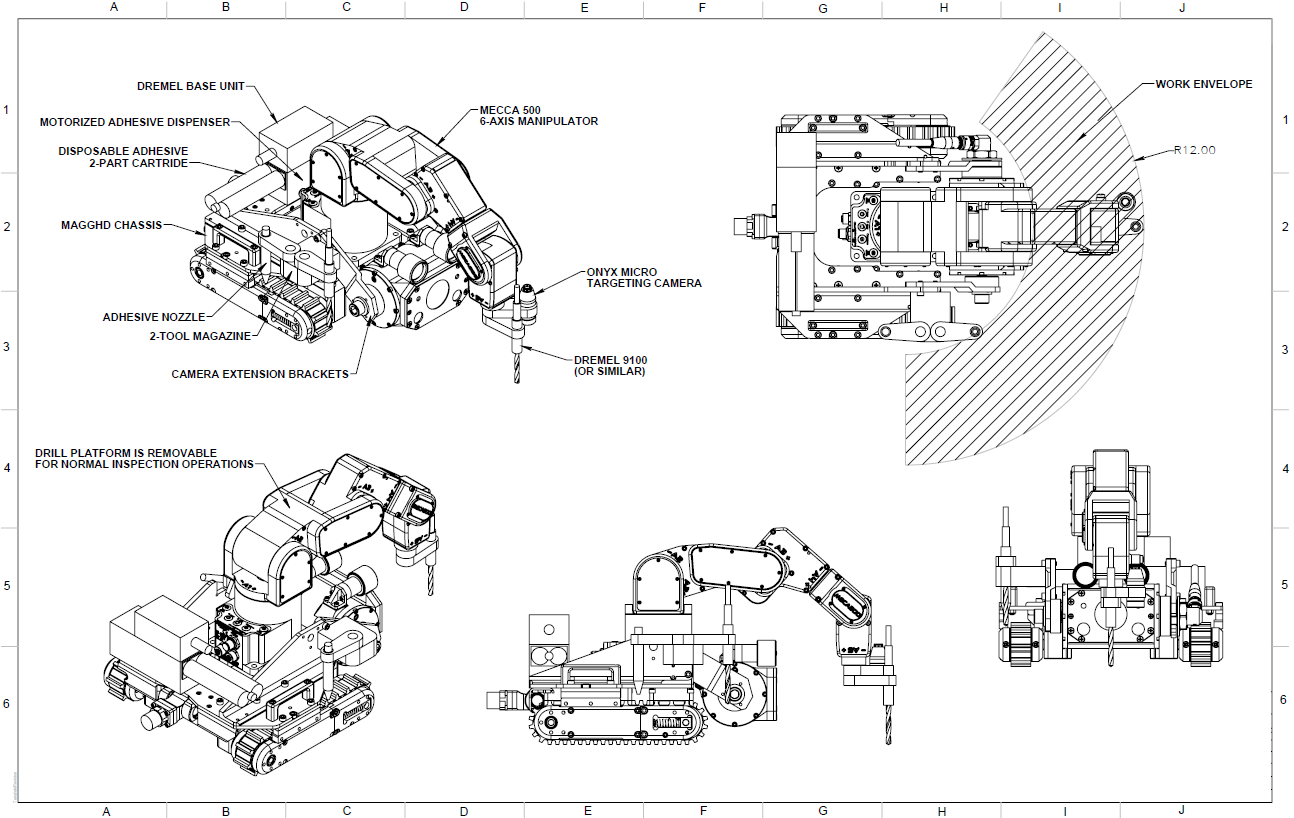
Eddyfi Technologies’ robotic platforms are regularly used for tooling and other bespoke remote operations. Numerous adaptations of the VersaTrax platform have enabled clients to overcome specific challenges never possible before. Proven in the renewable energy sector, the true potential of this technology is green.
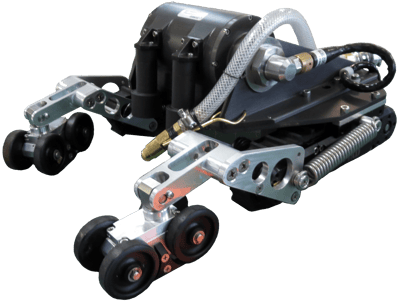
We invite you to contact our experts to discuss your specific requirements for robotic deployment that empowers safer, more productive, and sustainable operations today.