Composites enable lighter, robust structures with better protection against fatigue, impact, and corrosion – the ideal material for the aerospace sector. But with advantages of strength and light weight composite parts also comes increased manufacturing costs due to labor intensive techniques. Aerospace companies have previously been limited by suppliers unable to deliver parts, already carrying a higher raw material cost, in the volume required. The introduction of automation and robotics in composites manufacturing has resulted in higher productivity at lower costs. Aerospace manufacturers are now looking at automated inspection for the same benefits. With regulatory conditions to examine every single aerospace component, non-destructive testing (NDT) can slow down operations.
Naturally, we present the Beyond Current solution.
The desire to speed up inspection of composite parts is shared by most manufacturers. When you recognize the benefits afforded by industrial robotics employed for fabricating composite parts used in the aerospace sector, it’s not a far leap to consider them for new material verification and in-service aircraft or spacecraft integrity assessments. Automating what is currently manual NDT facilitates earlier damage detection and a deeper analysis of damage growth – quicker and cheaper.
Common defects that may form during the composite manufacturing process include porosity or voids in the material, foreign bodies, fiber misalignment or deficiencies, delamination, and bonding defects. With robotics carrying out ultrasonic testing (UT) during the trial process, it’s possible to collect more comprehensive data thanks to additional (less costly!) assessments. This helps engineers understand how composite parts will perform during operation and ultimately avoid uncontrolled damage development during their useful life.
The Panther™ 2 is designed for industrial applications, offering unparalleled performance in a compact desktop unit paired with an ultra-fast ethernet connection, an ideal solution for deployment in rough industrial environments where the instrument may be away from the acquisition computer. With the speed required for industrial integrated PAUT solutions, Panther 2 offers the most complete set of TFM imaging techniques, making it the ultimate tool for composite defect detection.
The Acquire™ software that controls the Panther 2 offers various industrial modes that help speed up inspections.
- Sequential mode: This is a simple electronic scan for which a single small aperture is moved across the entire aperture of the probe. This is the most common mode of inspection used by all manufacturers to perform normal incidence inspections.
- Mixed modes: The Panther 2 allows the use of eight simultaneous apertures identical to the one used in the sequential mode. In theory, it is possible to speed up inspection by a factor of 8. Crosstalk between the various apertures may affect how many apertures can be used simultaneously.
- Super-fast mode: A single plane wave is sent into the part and an electronic scan is performed in reception thanks to the parallel architecture of the Panther 2.
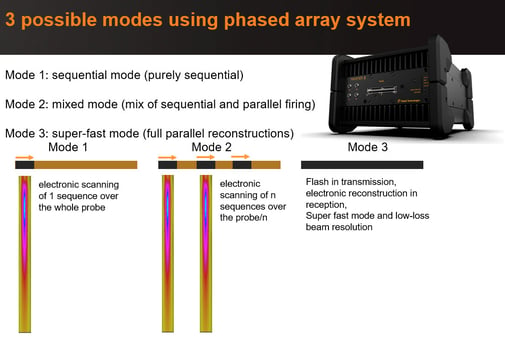
Let’s look at a schematic of the three modes in the following video. The clock on top shows the time required to perform the inspection for one mechanical position of the probe.
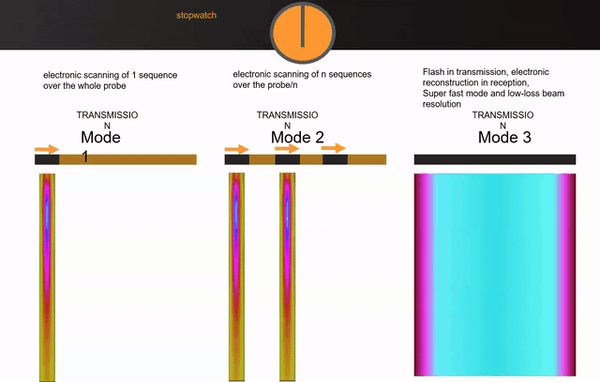
The first mode needs to scan the aperture across the entire array. For each excitation, the system needs to wait for the ultrasound to propagate inside the component before firing the next aperture. The second mode performs the same acquisition with up to eight apertures fired simultaneously. Finally, we can see that the super-fast mode is almost instantaneous as the system only needs to fire once. The limit in speed is dictated by the ultrasonic path and the PRF of the system (up to 40 kHZ). The following table compares the speed of the three modes for a 100-millimeter (4-inch) thick aluminum block used for calibration. Of course, speed depends on the thickness of the component under inspection as ghost echoes can appear for thick components.
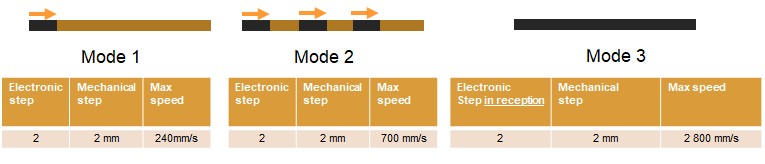
The following video shows the robotized inspection of a thick composite component using the mixed mode. This mock-up contains several flat-bottomed holes at various depths. The speedometer shows the reachable speed for this configuration. It is possible to move the probe up to 1200mm(26in) per second without losing any data.
Beyond inspection at the manufacturing stage, evaluation of in-service aerospace assets is necessary for monitoring the inevitable degeneration process. Defects may include moisture ingress, deterioration between the fiber and matrix interface, delamination, cracking, buckling or fracture of fibers, and bond failure. The Gekko® was the first portable unit with standard support for 3-axis encoding, making it possible to use with mouse type scanners for fast screening of large plates. It can map extensive composite components without needing to perform raster scans; acquisition is like painting the part with the probe. A typical wheel probe can be used with Gekko, acquiring data along a line; the clicker increments the scan to perform other lines and fill a C-scan. See how TFM paints the perfect picture here.
The time and cost savings offered by automation and robotic implementation of composite part inspection in the aerospace industry are undeniable. Eddyfi Technologies offers the advanced tools for repeatable, actionable, meaningful, and preventative data results. Request more information from one of our NDT experts to discover how we can deliver the relevant solution for your aerospace inspections today (and make sure you’re following our social media accounts to stay Beyond Current with even more related content).
View this post on InstagramA post shared by Eddyfi Technologies (@eddyfitechnologies) on