Corrosion scabs and blisters have always posed a threat to owners and operators scrupulously monitoring asset integrity and remaining useful life. The remaining ligament can be hard to estimate, scab removal is potentially hazardous, and there’s no universal method to characterize damage. Nonetheless, asset owners still require risk-based inspection for strong risk management and to ultimately see everything that’s coming with no surprises.
Current inspection methods have included visual assessment and pit gauging, ultrasonic mapping and laser scanning, or digital radiography. Each have their own disadvantages. The main challenge stems from the scab corrosion material itself. Without removing the scab, visual inspection, ultrasonic testing (UT) and laser scanning are unable to assess the structural damage of the component hidden under corrosion. Scab removal is a hazardous endeavor, especially for an in-service component that could potentially encourage a leak or further damage. Unfortunately, the height of the scab itself depends on so many parameters that we can’t rely on it to accurately determine wall loss.
One alternative that does not require scab removal is digital radiography. However, digital radiography isn’t going to give us the insights we need either. This method requires tangential shots which are not good on pipes that are larger than 150 millimeters (6 inches). Thick scabs reduce the contrast and therefore reduce measurement accuracy. This is in addition to the more obvious disadvantages related to health hazards and disruption of plant operations.
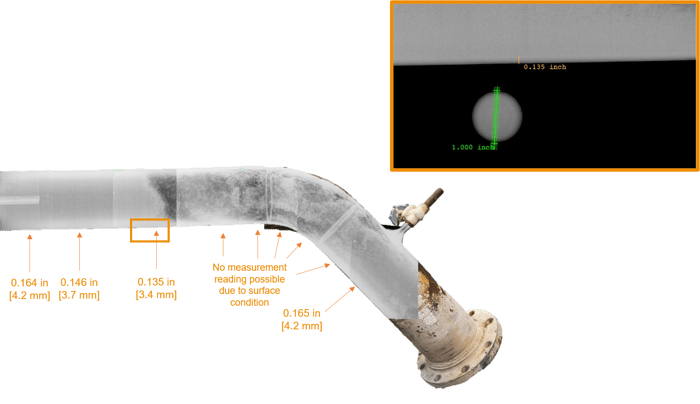
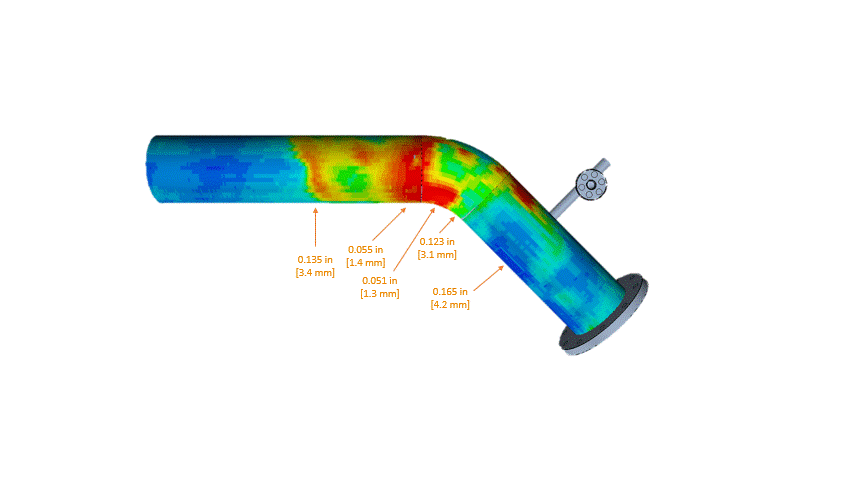
This is where Pulsed Eddy Current (PEC) testing comes into play. PEC has been recognized for its ability to detect and size corrosion through blistering and scabs in wall thicknesses up to 100 millimeters (4 inches), insulation as thick as 300 millimeters (12 inches), in pipes as small as 25 millimeters (1 inch) through metallic weather jackets and other interfering elements. However, a limitation of PEC is the difficulty in providing accurate wall loss estimation of very small defects. This is related to the sensing footprint of the probe, i.e. the area over which the wall thickness measurement is averaged — the smaller the footprint, the more accurate the results.
With a mission to solve industry problems by constantly pushing the limits of advanced Non-Destructive Testing (NDT) to new heights, our R&D experts have come up with a novel, patent-pending sensor design to improve Eddyfi probes’ footprint and provide a better estimation of the remaining ligament of very small flaws.
There is always a physical limit on how small one can make the footprint while maintaining the desired range of utilization (nominal wall thickness and acceptable liftoff). Previous attempts at focusing magnetic fields to achieve a smaller footprint resulted in solutions with drawbacks that negated all the benefits, making them unfit for use. This shows how truly difficult this endeavor is!
Our dedicated solution offers the best estimation of the remaining ligament, detects the smallest possible defects with PEC technology, offers top-quality data acquisition at high productivity rates and enables safe assessment of the remaining wall thickness over corrosion scabs. Not bad for a day’s work. The PECA HR probe consists of an array of dual sensors arranged in a specific configuration. An algorithm combines information from the sensors to achieve spatial triangulation and ultimately obtain a footprint that is significantly smaller than that of an equivalent conventional probe. In short, a smaller footprint = better detection and depth sizing accuracy. In practical terms, this new sensor can detect flaws half the size (in volume) compared to the previously available version technology.
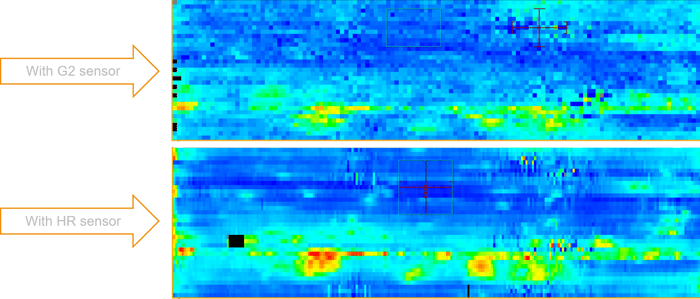
Comparative scan on a 7.8mm/0.3in NWT pipe covered with patches of scab
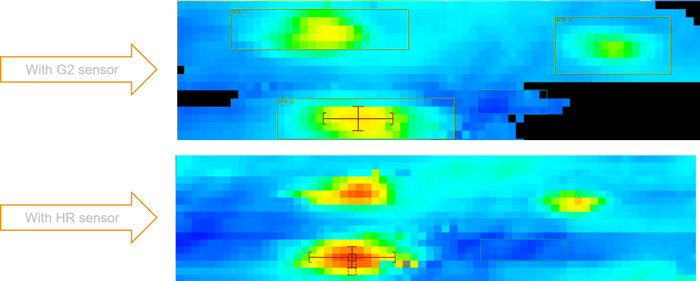
Comparative scan on a 6.35mm/0.25in NWT pipe covered with patches of thick scab
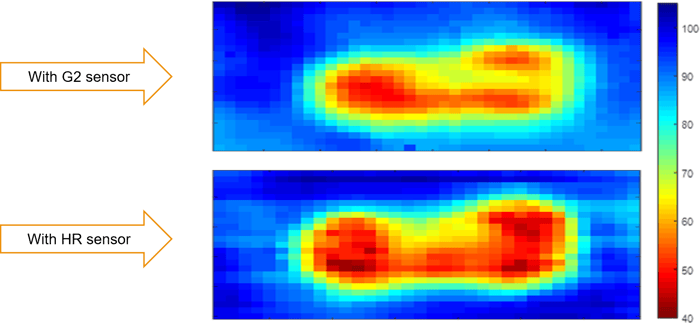
Comparative scan on a 6.35mm/0.25in NWT pipe covered with a 25mm/1in thick scab
An accessory called the Scab-Mat enables constant liftoff while providing a scanning grid and minimizing the disruptive effect of the corrosion material on the PEC signal. The PECA HR probe is part of the Eddyfi Lyft® inspection system offered by Eddyfi Technologies. This field proven instrument is the world reference for Pulsed Eddy Current testing.
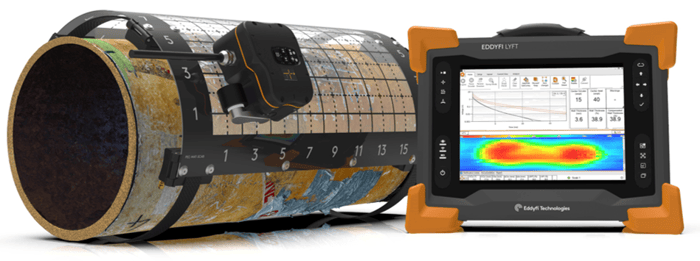
We’re solving the problems that others can’t with advanced NDT solutions, so you can feel confident and in control knowing that you can stay Beyond Current and see beyond the corrosion scab. Contact us today to discuss your asset integrity assessment requirements.