If you’re reading this, we probably don’t need to tell you exactly how challenging ultrasonic testing of nozzles can be. In order to accurately capture indications, a skew must be applied to the UT probe so that the inspection plane is perpendicular to the defect. Several flaws are extremely sensitive to beam orientation, re-confirming the need for skewing the beam. Furthermore, defects near the surface typically requires beams to reflect off the backwall – not exactly easy when vessels are curved.
We’re here to let you know we’ve simplified nozzle inspection with the power of augmented reality (AR). AR is increasingly prevalent in our everyday lives and as it matures, the applications for enhancing user experience across industries is also growing. The non-destructive testing (NDT) sector isn’t exempt, and Eddyfi Technologies continues to keep its stakeholders Beyond Current.
Capture™ software, embedded in portable phased array UT (PAUT) flaw detectors, features a unique application designed specifically to help technicians inspect nozzles. It enables operators to define a nozzle directly in their M2M Gekko® or Mantis™, designate the course around the nozzle, use three-axis encoded scanners to look for skews, and probably the greatest benefit: display a live cross-section superimposed on sectorial data from the three encoder inputs.
While it’s not always feasible to use scanners with limited access or small nozzles, having a cross-section still provides the same benefit. Inspectors can manually enter the position of the probe and Capture will generate a corresponding cross-section to assist with probe positioning and indication assessment.
When using an encoded scanner for nozzle inspection, skew needs to be considered and therefore, three-axis is sometimes required for rotation around and translation toward the nozzle as well as probe skew. The Gekko and Mantis readily support commercially available three-encoded axis scanners for PAUT nozzle inspection; they enable calculating the helpful overlay in real-time with rebound off the backwall of nozzle from the nozzle side. This hardware pairing tied with our software solution just might be your new best friend.
It’s a bad day to be a hiding defect.
Capture permits folding the data in order to correctly position Lack of Penetration (LOP) along the pipe backwall. It can be further characterized with height measurement.
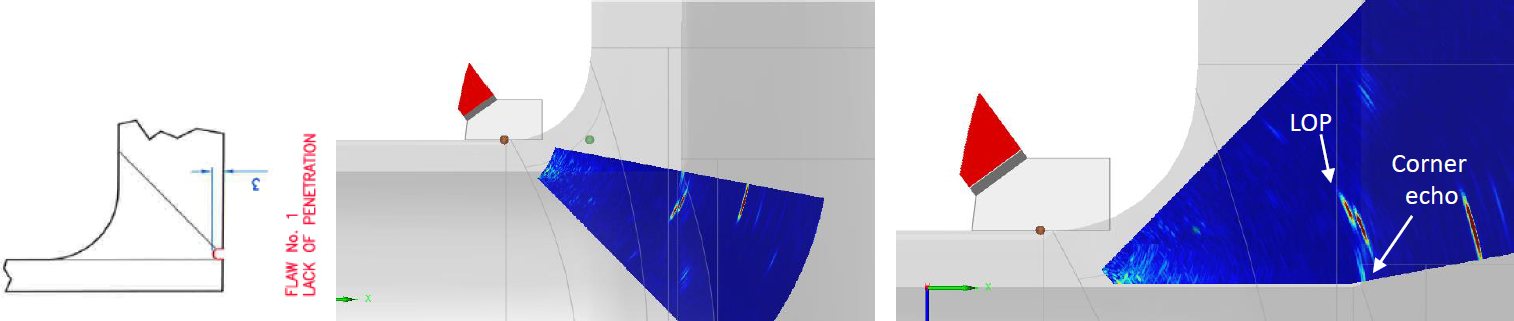
A folded sectorial scan accurately positions the corner echo and the weld root. With tip diffraction visible, cracks can further be defined.
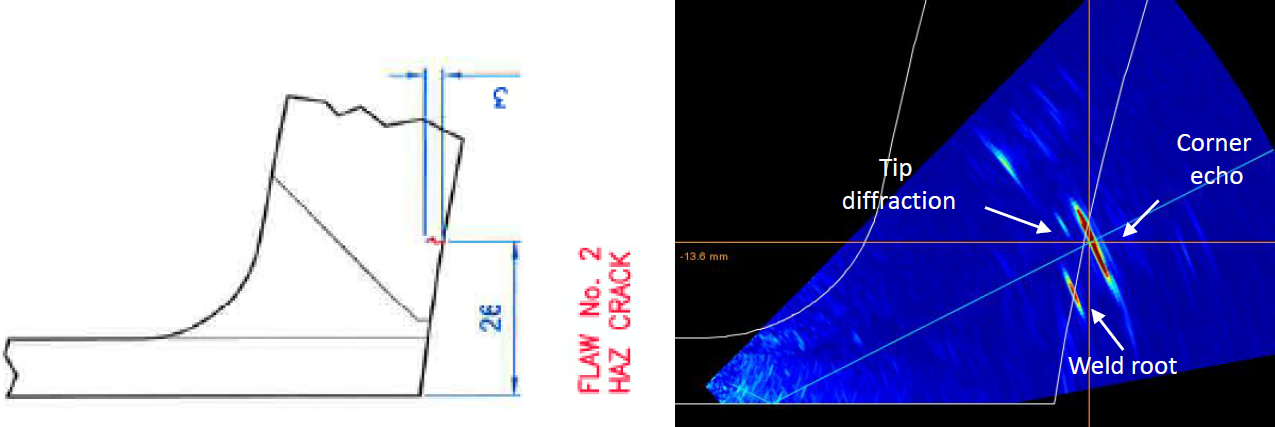
It’s possible to see two diffraction echoes derived from each point of the crack. This supports center line crack height measurement.
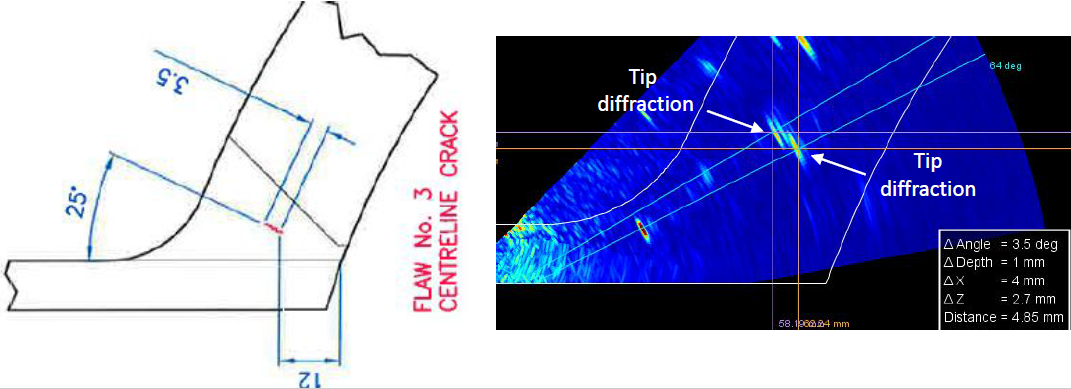
Two strong echoes can be detected in the presence of slag.
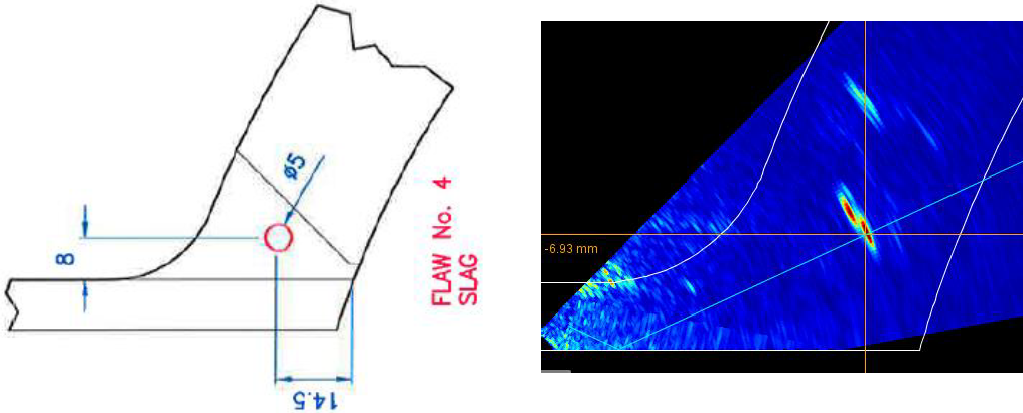
A strong echo along the backwall of the main pipe can be observed with lack of root fusion. It aligns with the nozzle axis, enabling additional characterization.
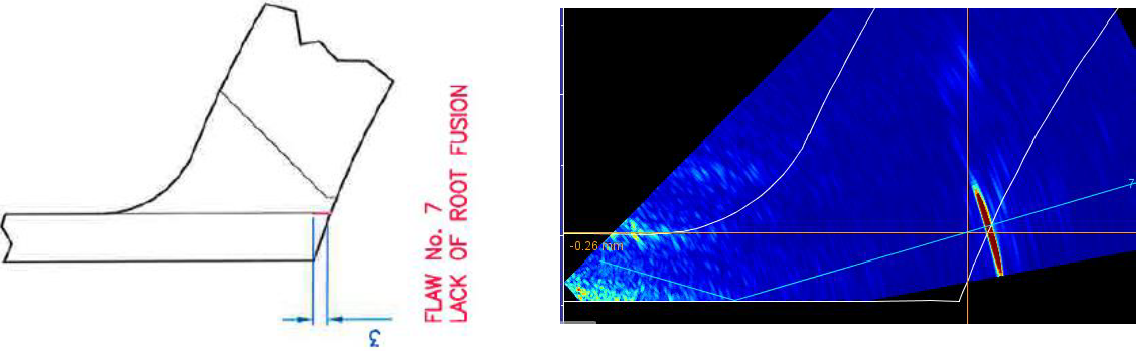
Enlight is M2M software that allows further analysis of data acquired during your nozzle inspection. It can be used to predict and design the best scan plans to inspect a given nozzle. With all views available and fully exportable into a 3D view, it helps you understand echoes. Whichever way you look (S-scan, B-scan, D-scan, C-scan…), we’ve got you covered for making the right call.
The benefits of augmented reality with live overlay of the nozzle slice with PAUT data are undeniable. Why not contact us today to take the next step in simplifying your otherwise cumbersome nozzle inspections?