Carbon fibre spars were inspected by NDT service provider MME Group1 based in the Netherlands. These components are used as masts on the ultra-fast sailing ships of the Volvo Ocean Race. The requirement for quality is evident as winning the race is at stake and the safety of the people on board the vessel is paramount. The inspection was carried out with a Gekko® phased array system designed, built, and supplied by Eddyfi Technologies.
Historically, the materials used for spars were made from wood which was replaced by aluminum in more recent times. In the search for lighter and stronger materials, carbon fiber spars are being produced for this purpose. The advantage of a carbon fiber spar is that it is only 60% of the weight of an aluminum spar, while having equal or better strength and stiffness properties.
Strength-to-weight ratio is critically important. The weight reduction strongly aids the boat's lower gravitational point, resulting in higher speeds and better boat balance and stability. This carbon fiber, lightweight material is gaining popularity for obvious reasons. It is also widely used in the aerospace, aviation, and automobile industries, plus numerous other applications.
The production of carbon fiber spars starts with winding resin-soaked carbon fibers around an aluminum mandrel. The carbon fibers are wound in different directions to improve the spar's strength and multi-directional stress loading properties. When all the carbon fibers are laid down, the air must be squeezed out. This task is completed using a heat shrink, after which the spar is placed in a vacuum bag. The whole spar is then placed in a giant oven, called an autoclave, for about eight hours to cure the epoxy.
With the use of new materials also came the new inspection requirements. In the absence of proper inspection equipment, the wooden masts of the old days were inspected with a simple hammer tick. The acoustic response produced was assessed by a person trying to find impurities in the wood that could lead to failure under the heavy stresses related to sailing under the more challenging conditions. With the introduction of aluminum spars, inspection using ultrasonic testing (UT) became a possibility. The quality of ultrasonic inspections has drastically improved over the years. The introduction of phased array UT (PAUT) makes the inspection a lot faster than a single probe ultrasonic inspection, aiding the possibility to make inspections possible on more complex materials.
As mentioned2,3, carbon fiber composites are being widely used in various industrial areas including aerospace, automobile, and other fields because of their advantages in mechanical properties and structural functionalities. The use of carbon fiber reinforced polymer, or CFRP, composites is increasing year by year due to its excellent mechanical properties such as low weight, high specific strength and stiffness, and exceptional fracture resilience. Typical for the maritime market, there is an additional benefit: excellent corrosion resistance and durability. However, the production of these carbon fiber materials could also produce defects that will undermine all the good properties of the carbon fiber material. Defects2 include delamination, inclusion, cracks, curing, void, debonding, and are also called matrix defects. Most of these defects are detectable using a proper ultrasonic technique and setup. The Gekko, in this case, is very well equipped to properly inspect carbon fiber spars or other CFRP components.
.jpg?width=400&name=MME_HallSpars_PA%20(10%20of%2015).jpg)
The Gekko used was one of the recent models. The advantage of using a Gekko portable instrument, or other Eddyfi Technologies phased array inspection technology, is that the equipment continually evolves with the technology's current state of the art. The NDT technician stays Beyond Current and benefits from the latest tools developed for corrosion mapping, something widely used in many industries for this particular inspection. Also, for the final data and inspection analysis, the Gekko has some great tools for automated defect analysis.
The most recent software version allows for, among many more other features, the use of floating gates, gate synchronization, etc. The option for floating gate analysis allows the user to capture thickness data (or disbonding, lamination, voids, etc.) if the ultrasonic response falls below the gates previously set. The floating gate option will then drop the gate relative to its previous height to try and capture data from the response. This will result in a massive improvement of poor ultrasonic responses either caused by material attenuation or corrosion effects. The mentioned option for automatic defect analysis greatly impacts the overall inspection efficiency when it comes to analyzing defects found. This specific feature will help the inspector get all the information on a defect by drawing a simple box around the defect area visible in the ultrasonic data. The defect will then be automatically added to a defect list with its width, height, and depth information. This defect information will then be directly available in a report that can be printed directly from the Gekko together with all its setup and calibration information.
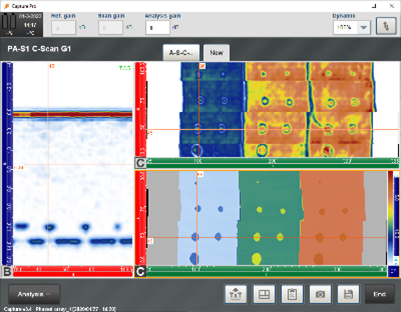
For me, this was an enjoyable project, and Eddyfi Technologies thanks MME Group for sharing this great application with us.
Check out this article on what you need to know about GFRP and CFRP inspection using ultrasonic methods, and get in touch with our team of friendly experts ready to answers your specific questions.
1 Ensuring ocean race spar quality, 2 Carbon fiber testing, 3 Carbon-fiber-reinforced polymers