Complex components can be challenging to inspect due to the difficulty in finding a proper scan plan. Undesirable echoes coming from various places in the geometry make analysis complicated and tedious. We previously demonstrated how to define TKY welds and nozzles in Capture™ software, and this blog focuses on the import of 2D CAD overlays.
Many of today’s inspection issues are due to geometric constraints. Phased Array Ultrasonic Testing (PAUT) and Total Focusing Method (TFM) can provide images but without a visual aid, it may be difficult for operators to interpret the various echoes seen on screen. Echoes may come from indications but also the geometry itself which leads to a potentially high rate of false alarms. Capture offers the ability to import 2D CAD files and superimpose the ultrasonic data, PAUT and TFM, on top of the cross-section of the part under examination. This helps operators precisely position any indications and distinguish between geometry echoes and echoes coming from defects.
In the specimen definition, operators can import CAD files for plate and pipe geometries meaning that Capture will extend that profile as a linear extrusion or a revolution extrusion, respectively. In the following image, we imported the profile of a stainless-steel weld. The backwall is tapered and the weld is discretized in various volumes to represent the various welding passes. The operator can adjust his delay laws with focusing points properly positioned to maximize the sensitivity of detection along the opposite side, for example.
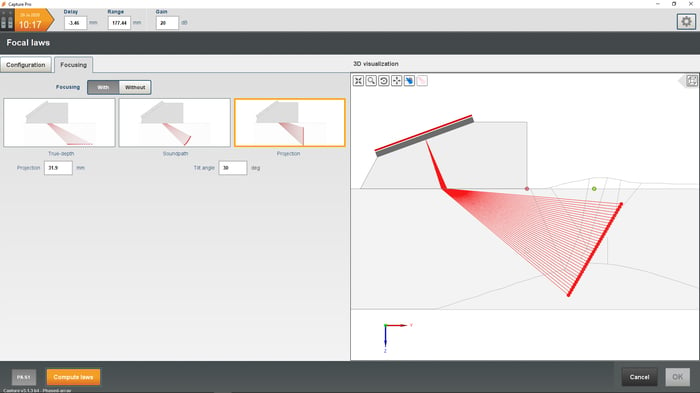
Let’s look at an application for a train axle inspection, importing the CAD of the axle. We positioned the probe at one end of the axle, and the delay law is a sectorial scan with a projection focusing along one side of the axle to maximize the sensitivity of detection.
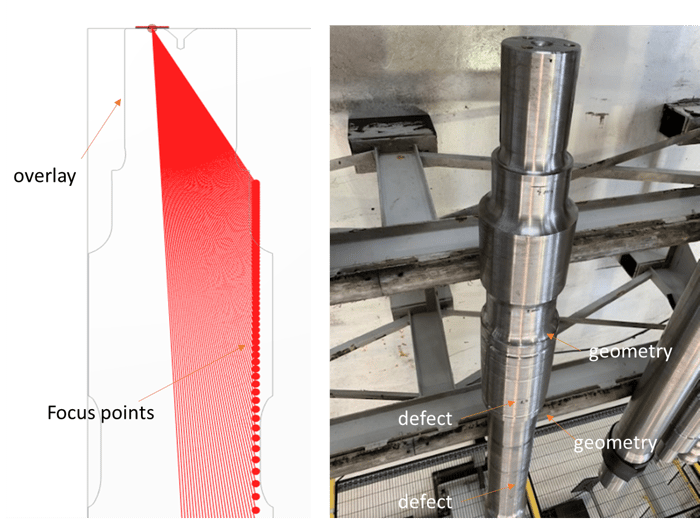
The following image is the sectorial scan (S-scan) obtained superimposed with the overlay of the axle. Many echoes are observed making it difficult to identify them individually. The overlay allows clear identification of the geometry and defect echoes as they are properly aligned with the cross-section of the component. The geometry echoes visible in the sectorial scan correspond to the geometry indicated in the photo of the axle. Notice that the defect identified at the bottom of the S-scan is located 1200 millimeters (47 inches) from the end of the axle, and it is detected with a 26 dB Signal-to-Noise Ratio (SNR). Optimizing the scan plan with the right probe and delay laws provides optimum detection of defects located far away from the probe.
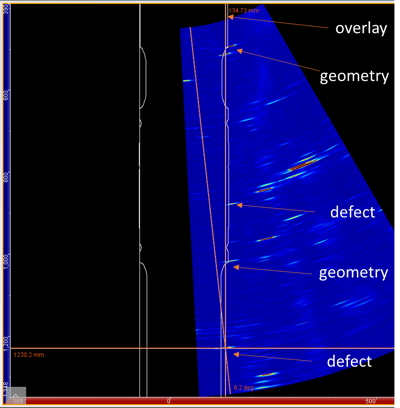
The following S-scans illustrate two more examples of the CAD overlay obtained for a blade and rotor during a turbine inspection. Both CAD files of the blade and rotor were imported into Capture and the index offset of the probe set to align the geometry echoes with the overlay of the part. Defects can then be seen and positioned properly into the referential of the components, giving position and sizing information which is crucial for Fitness-For-Service (FFS) analysis.
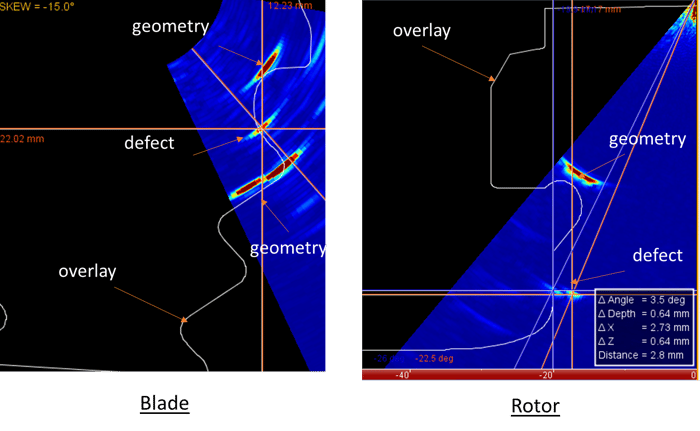
Finally, we illustrate the CAD import capability with a TFM acquisition. The following image shows the TFM image of an IIW TYPE 1 mockup using a 128-element 2 MHz probe with 256k pixels. The overlay of the mockup was imported, and the probe centered on the top surface. Notice that the TFM was done with the full 128-element aperture, which is unique to the M2M Gekko® instrument.
You can see reflections coming from all features of the block: the 100 millimeter (4 inch) radius on the left, a 25 millimeter (1 inch) radius on the top right, the notch at the bottom as well as the 1.5 millimeter (0.060 inch) diameter side-drilled hole at the bottom right. They are all properly aligned with the cross-section of the IIW mockup.
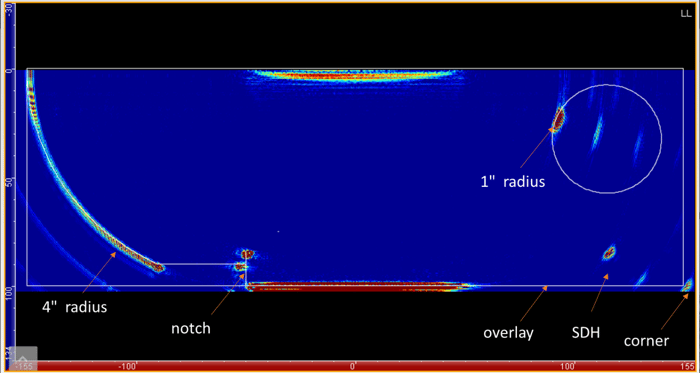
The ability to import complex profiles in Capture software can help operators set the proper scan plan to obtain better sensitivity and better sizing capability. Overlays of components are important for the interpretation of all the echoes allowing operators to distinguish between indications and geometry.
Stay Beyond Current and contact us to learn more about the M2M Gekko and Mantis portable instruments for your complex component inspections today.