Here’s the Problem
In recent years, concerns have been raised regarding the safety of technicians present on aging aboveground storage tank roofs composed of hundreds of thin steel plates welded together. Different damage mechanisms, including vapor space corrosion, can reach to an extent where it is no longer safe to walk on the roof plates without risk of an incident. Unlike floor plates, generalized corrosion is the main concern for roof plates. The API 653 general requirement for tank roof evaluation is that:
"Roof plates corroded to an average thickness of less than 0.09 in. in any 100 in.2 area or roof plates with any holes through the roof plate shall be repaired or replaced."
Current inspections involving ultrasonic testing measurements on roof plates are often limited to a few measurements per plate. Often, one measurement at each corner and one in the center will be used to assess the average wall thickness of the plate. This technique may leave corroded areas greater than 100 in.2 undetected. EMUUA 159 makes recommendations for UT measurements to be performed on the roof over radial lines, again with limited coverage, increasing the risk of leaving generalized corrosion undetected.
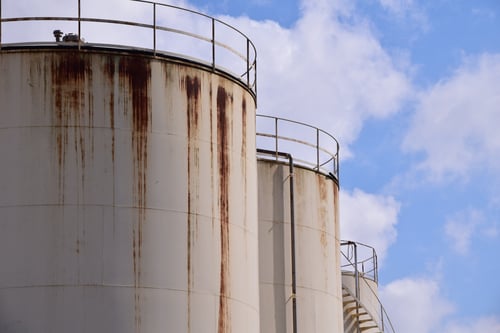
Some asset owners decide to plan more thorough inspections than simple spot checks. In some cases, nearly 100% of the tank roof surface is inspected using either MFL floor scanners or UT corrosion mapping crawlers. In the first case, the weight of the scanner may be of concern when looking for significant generalized wall loss. Furthermore, MFL is best suited to find small, localized indications rather than generalized corrosion. Complete UT corrosion mapping on the other hand offers optimal detection and accuracy but also limited productivity. Uneven surfaces due to a thick paint coating along with thin plates also make UT measurement challenging.
The limitations of currently available techniques and the rising concerns over personnel safety lead to the quest for a fast and efficient tool that will assess the remaining wall thickness of tank roof plates in real-time without requiring heavy equipment. This article presents the results of a proof-of-concept trial to evaluate if Pulsed Eddy Current Array (PECA™) can be used to address this challenge.
The Beyond Current Solution
In recent years, pulsed eddy current has been increasingly used in the field to inspect insulated and fireproofed assets for corrosion. This technique is resilient to liftoff variations and poor surface or paint conditions. This resilience has fueled the rise of PEC in new applications as a screening tool that requires no surface preparation over painted or coated surfaces that do not necessarily have significant liftoff.
Figure 1: The PECA-6CH-MED covers 457 millimeters (18 inches) on flat surfaces and pipes down to 150-mm (6-in) OD
Pulsed eddy current array sensors are now available with up to 457 millimeters (18 inches) of coverage. This technique can be used for the screening of large areas of corrosion where UT would be traditionally limited to spot check measurements. Torngats, a Canadian service company, decided to try the technology to assess corrosion on tank roof plates. Two plates with known corrosion were selected for the trial. The roof was originally installed in the 1950s and the plates nominal wall thickness is 4.76 millimeters (3/16 inches).
Figure 2: PEC trials on aboveground storage tank roof
Since PEC provides relative wall thickness measurements, calibrating the tool on a nominal section or validating the calibration area thickness is essential to ensure accurate measurements. In this case, the plate presented general corrosion with no area showing more than 3.3-millimeter (0.130-inch) wall thickness. This value was used for the calibration.
Figure 3: PEC C-scan of tank roof plate showing extensive corrosion
One of the plates showed two zones with over 100 in.2 in area and less than 2.29-millimeter (0.090-inch) remaining wall thickness which is the repair threshold identified in API 653 for tank roof inspections. Similar damage extent had been identified during an MFL inspection prior to the PEC trials.
The PEC data also shows the presence of support members (rafters) under the tank roof skin. The rafters create a mass effect that is visible on the PEC C-scans but did not prevent the detection of large corroded areas which spanned over the rafter region.
Figure 4: Mass effect from rafters
The Benefits of PECA
Pulsed eddy current array demonstrated its ability to detect and assess generalized corrosion on tank roof plates. When calibrated in an area of known thickness, the technique enables the assessment of the absolute remaining wall thickness of the tank roof plates with a typical accuracy of ±10% of the nominal wall thickness. Areas with damage beyond the repair threshold can be assessed in real-time.
Weighing only 7 kilograms (15 pounds), the PECA probe is significantly lighter than MFL scanners, further mitigating the risk associated with using heavy equipment on tank roofs.
The real-time assessment of the remaining wall thickness ensures that technicians can evaluate the safety level of the area directly in front of them as they are carrying out the inspection, increasing operator safety. Furthermore, the technology could be combined with a remote deployment solution to further reduce the risk to operators.
PECA also enables the combination of high coverage with productivity. On 4.76-millimeter (3/16-inch) thick roof plates, scanning speeds are on the order of 100 to 200 millimeters (4 to 8 inches) per second while covering 457 millimeters (18 inches). This productivity enables inspecting 100% of the plate surface, ensuring a higher PoD than conventional UT spot checks.
Unlike other electromagnetic techniques, PECA technology is also sensitive to relative changes in wall thickness, whether they are characterized by a sharp or slow transition from nominal, ensuring that even generalized corrosion is accurately assessed. Furthermore, since PEC is not affected by poor surface conditions, it requires no surface preparation to perform the inspection.
Conclusion
With increasing concerns over the safety of technicians on tank roofs, new methods are being considered to ensure the detection of generalized corrosion. PECA combines high productivity with sensitivity to generalized corrosion and optimal coverage. It provides real-time thickness readings and presents an interesting alternative to traditional UT or MFL inspection of aboveground storage tank roofs plates. Get in touch to discuss the best options for your next inspection campaign today.