Over the past years, Eddy Current Array technology (ECA) has been progressively gaining ground in the aerospace, energy, power generation, nuclear and chemical industries, amongst others. What do these sectors have in common? Welds! All of these industries, and many others, rely upon strong, dependable welds in order to operate efficiently and safely. Discover how ECA can help increase confidence in weld quality by not only meeting, but often surpassing, the inspection requirements in this article.
Considering how ubiquitous welds are to such aforementioned critical infrastructures, there are ample opportunities for various welding defects in even the most stringent of regulatory environments. Lack of fusion (LOF), lack of penetration (LOP), porosity and inclusion are just four among many examples of weld defects that can threaten the integrity of the very structures they’re meant to support. Furthermore, welds of questionable integrity have a tendency to develop fatigue cracks with continuous load bearing. That being said, weld inspection has quickly become a must in order to guarantee the integrity of such critical structures. ECA is used to efficiently inspect various weld material and types, including orbital welds, friction stir welds, butt welds, fillet welds, and electric resistance welds (ERW). Let’s explore the main parameters to consider before selecting the right ECA weld probe. Then, we’ll cover three weld types that ECA is more suitable for than you may think!
When thinking about inspecting a weld with ECA, some crucial key points need to be considered to select the appropriate probe type:
1. Surface condition and weld type
On smooth, or ground flush welds, the lift-off variations are often very small. Hence, increased sensitivity to small indications can be achieved assuming the right topology and size of sensor are selected. On the other hand, for butt welds, rougher surfaces or low-quality welds, geometrical variations in the weld can drastically reduce performance. Other electromagnetic technologies such as ACFM can be used on rough weld conditions.
2. Smallest defect to be detected
The size of the coil should be selected as a function of the defect size that is to be detected. The smaller the eddy current sensor the more sensitive it will be in detecting smaller defects. However, this also means it will be more sensitive to lift-off and geometrical variation! Compromise is sometimes required.
3. Alloy
The alloy of the weld and the base material (the two parts welded together) are to be taken into consideration when selecting the right ECA probe. As a quick reminder: on non-ferromagnetic alloys, surface breaking and subsurface defects can be detected. On ferromagnetic alloys, surface defects can be detected.
4. Changes in the material properties
The level of ferromagnetism, the welding process (heat, friction, etc.) and the alloy mix itself arrangement may introduce a noise to the eddy current signal. In both cases, such noise can often be managed with optimization of the ECA probe frequency and setup.
Butt welds & fillet welds – Ferromagnetic & Non-Ferromagnetic
Butt welds are the most popular weld type and are widely employed in many of our most familiar infrastructure staples from spent fuel pools in the nuclear industry to pipelines to the very buildings that provide our shelter and safety. The example below shows how an adapted ECA probe can easily conform to the surface to facilitate inspection while minimizing lift-off variation.
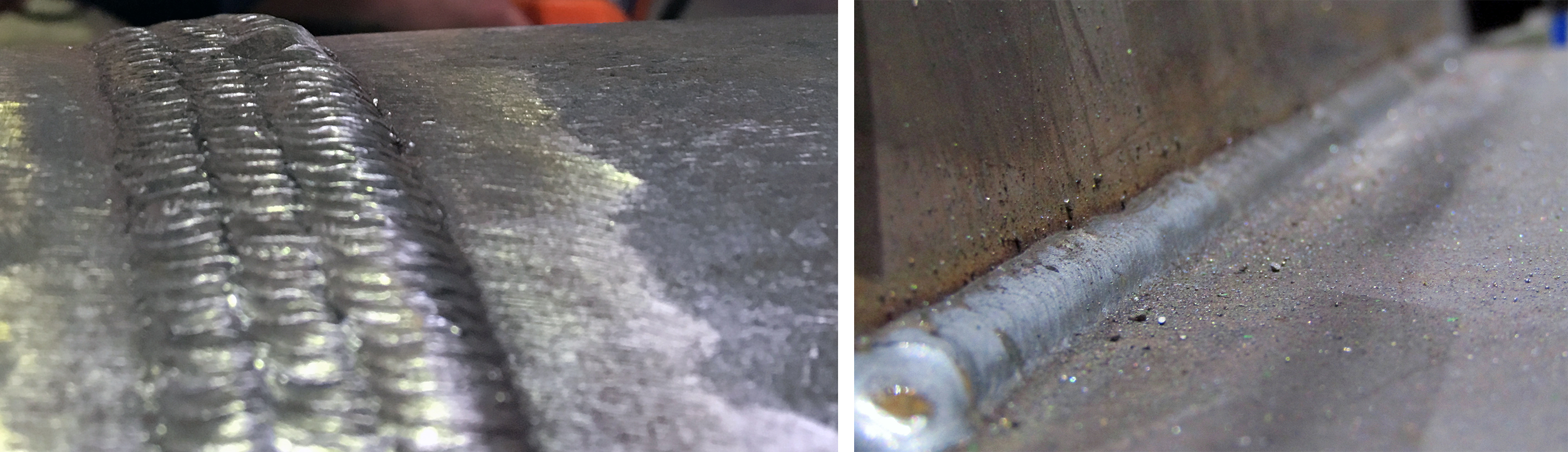
Important factors:
1. Condition of surface and weld geometry: Fillet weld & butt weld, relatively rough
2. Defect type: Cracks
3. Alloy: Carbon steel, stainless steel, and other alloys
4. Changes in the material properties: Relatively noisy
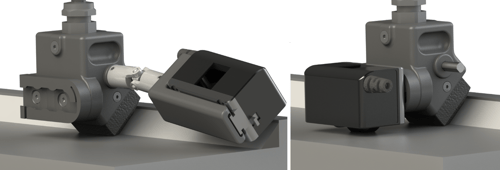
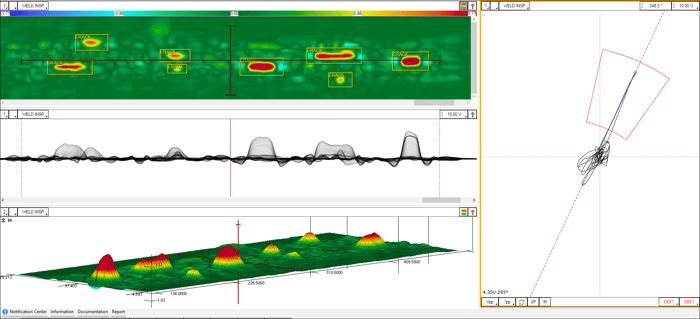
Tangential Eddy Current Array (TECA™)
Sharck™ is specifically designed for cracking in carbon steel using Tangential Eddy Current Array technology. These probes can detect cracks, measure their length, and size them as deep as 7 mm (0.28 in). Unlike more conventional techniques, this can be achieved without removing paint or protective coatings.
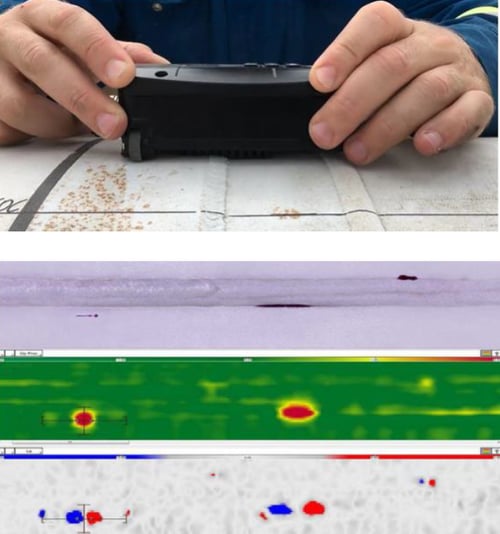
How does it work? Traditional pancake coil axes are perpendicular to the surface under test. TECA, on the other hand, uses tangential coils positioned on their sides, their central axes parallel to the surface under test. Eddy currents also flow parallel to the surface, making them capable of “diving” under cracks. Find out more on the TECA technology page.
Alternating Current Field Measurement (ACFM®) Technology
As previously discussed, surface conditions and weld geometry often pose a significant challenge when attempting to evaluate the integrity of a weld. Such is frequently the case in the railway, civil structure, offshore and underwater industries. For these applications, ACFM technology. has proven to be a reliable solution when surface conditions are a challenge or suboptimal for ECA. Furthermore, ACFM provides a depth measurement that can be used in both stainless as well as carbon steel.
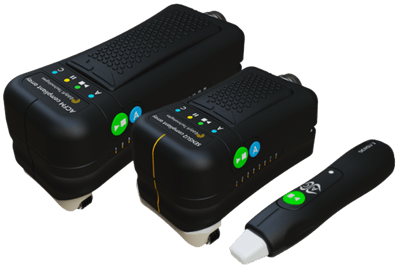
Friction stir welds – Non-ferromagnetic
Friction stir welds (FSW) are another weld type that lends itself extremely well to structural analysis using ECA probes. Many ECA probes have been successfully used in this field to ensure the integrity of such important structures.
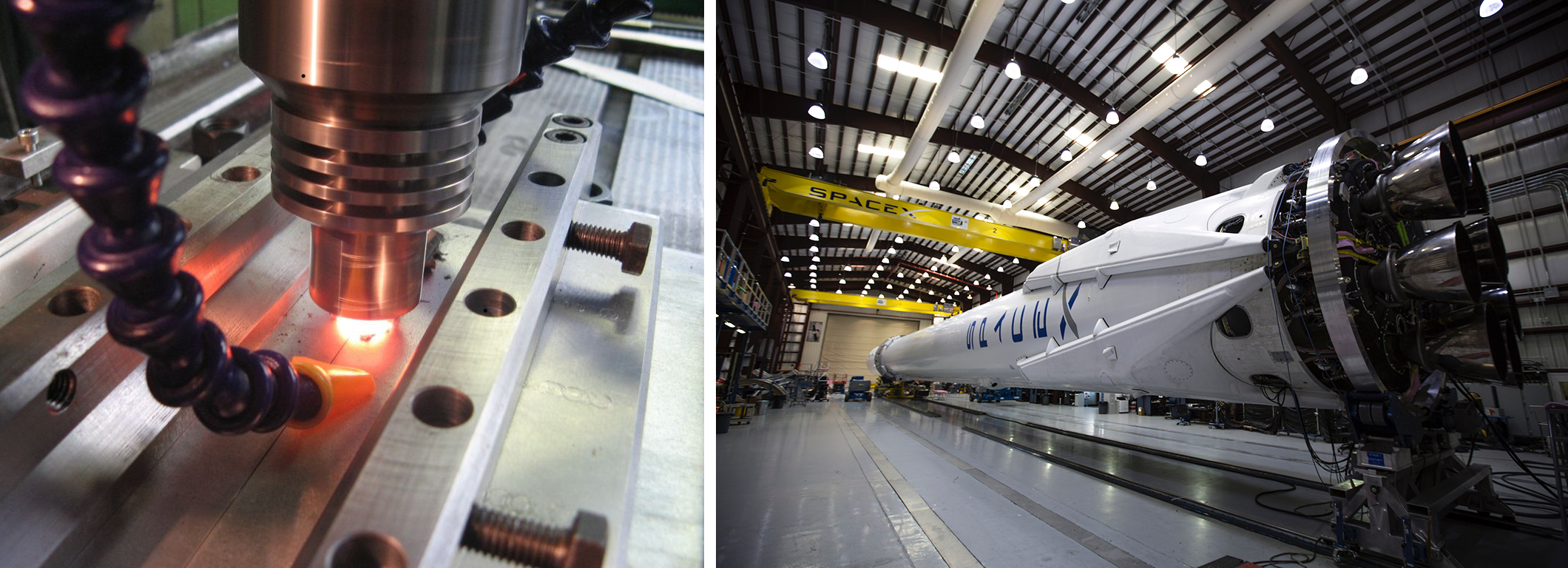
Important factors:
1. Condition of surface and weld geometry: Smooth, very light weld cap
2. Defect type: Cracks, LOF, LOP
3. Alloy: Aluminum
4. Changes in the material properties: Very light
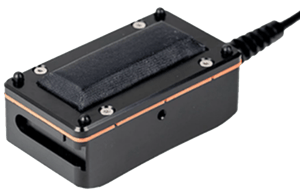
ECA padded probe
Here’s the ECA results on a lack of fusion in an aluminum weld.
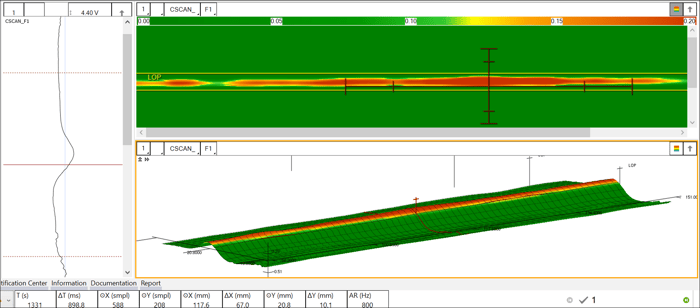
For more info on what ECA can do for FSW, click here.
Orbital welds – Non-ferromagnetic
Orbital welds are often used in the aerospace industry because of their precision and low profile. These high-quality welds are most often found in fuel, hydraulic, and brake lines as well as other critical components. The result is a small circumferential weld, with a minimal or non-existing weld cap.
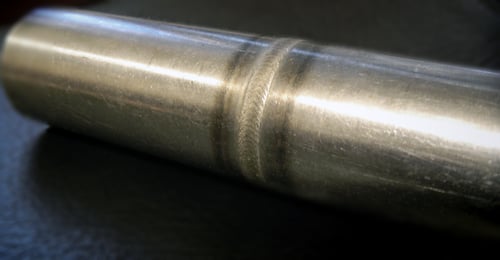
Let’s consider the 4 important factors we previously presented, applied to the orbital welds.
Important factors:
1. Condition of surface and weld geometry: Very smooth
2. Defect type: Sub-millimeter porosities, cracks, inclusions. Surface breaking & sub-surface.
3. Alloy: Titanium & Stainless
4. Changes in the material properties: Practically non-existent, very light
In such ideal conditions, the detection of very small defects becomes possible. Here’s the ECA results on a 0.25 mm (0.01 in) subsurface porosity, in a titanium orbital weld.
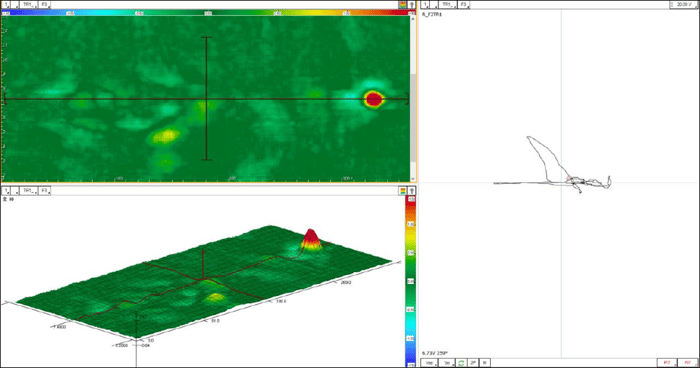
Custom capabilities, software, and tools to help analysis
Eddyfi Technologies can also develop tailored solutions for specific weld types, all of which are fully compatible with our high-end software. With its assisted analysis tools, Magnifi® can rise to the occasion and provide consistent and reliable results for almost any weld challenge.
For any and all questions, don’t hesitate to contact one of our experts!