Solutions for the inspection of online pressure vessels continue to be explored by large asset owners in the petrochemical industry. Owners have employed various methods of ultrasonic testing to help determine the real-time condition of pressure systems and provide fitness-for-service calculations for remaining life assessments (RLA). Eddyfi Technologies was invited to demonstrate a brand new advanced non-destructive testing solution directly relevant for online vessel inspection.
Common to the petroleum refining and chemical processing industries, various storage tanks, boilers and heat exchangers are designed to contain contents under extreme pressure. Given their critical function, it is imperative to monitor the structural integrity of pressure vessels to prevent a failure leading to a catastrophic disaster. Ultrasonic corrosion mapping has been a widely accepted alternative to vessel entry for over a decade. Ultrasound provides accurate wall thickness measurements of vessel shells and can determine the through wall extent of corroded areas. With the introduction of robotic crawlers and dedicated software platforms, ultrasonic readings with presented data sets has enabled a significant improvement in accurate results. Enhanced precision and positioning allow operators to accurately determine defect locations. Periodic inspection sets can be overlaid, and corrosion rates quickly assessed visually. Inspection robotic systems are becoming universally recognized and accepted.
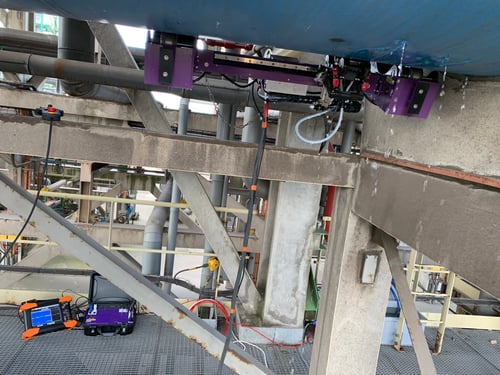
Eddyfi Technologies demonstrated the capabilities of its recently launched RMS PA system, the combination of the field proven Silverwing RMS automated crawler with the market leading phased array flaw detector, the M2M Gekko®. An event hosted by SPRINT Robotics at Total OLEUM Refinery in Dunkirk, France, afforded the opportunity to demonstrate how this unique offering allows operators to rapidly inspect pressure vessels for corrosion, erosion and other in-service damage mechanisms. Phased array technology is rapidly becoming a trusted method for volumetric inspection with typical applications for weld inspection and crack detection, and the RMS PA offers a fully integrated phased array corrosion mapping solution. Event spectators were able to witness firsthand the benefit of the RMS PA utilizing an effective 60mm wide ultrasonic beam that can collect A-scan information every 0.5mm for 100% coverage of the inspection area – in this case, two offline pressure vessels.
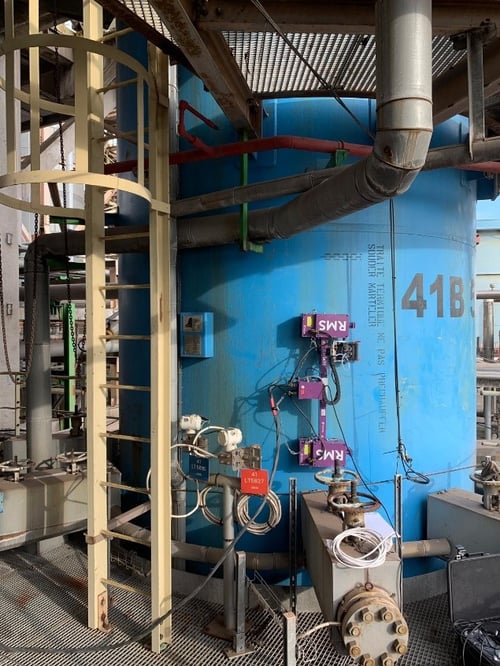
Inspection results were very encouraging for the RMS PA. Using phased array in lieu of a conventional ultrasonic probe helps significantly increase productivity and coverage without sacrificing resolution and image quality. Colour coded thickness maps instantly identify areas of reduced wall thickness that is the result of in-service corrosion. The image below shows the isometric drawings of the vertical vessel (left) and the locations of the collected corrosion mapping data sets (right).
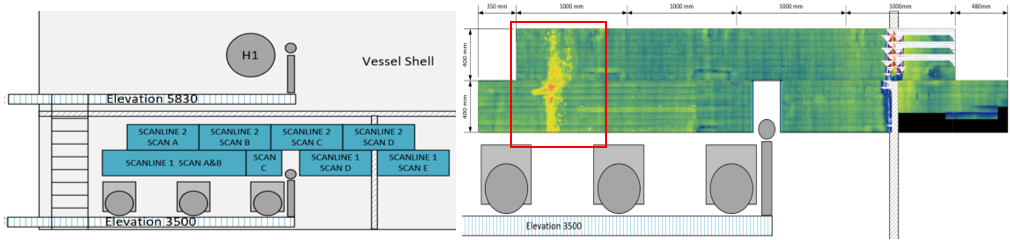
The image below shows the isometric drawing of the horizontal vessel (left) and the locations of the collected corrosion mapping data sets (right).
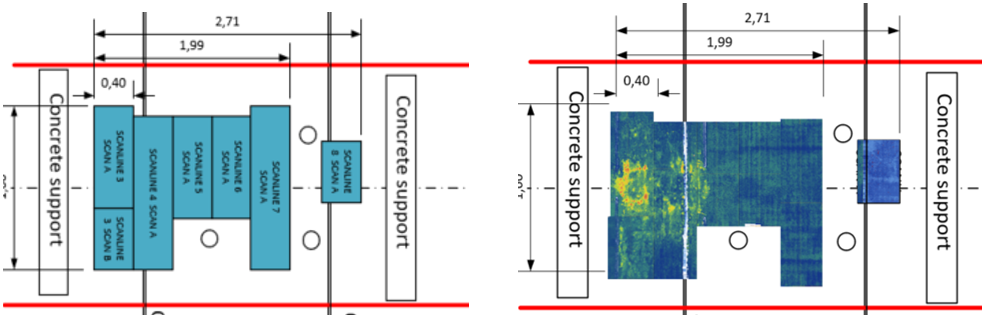
Identifying areas of damage from in-service operations is the primary function of a corrosion mapping survey. However, another benefit of using phased array technology for mapping pressure vessels is the level of detail found on internal attachments. Attachment welds can cause concern as pressure points and accurate engineering drawings are often not available for assessment. Using an amplitude-based C-scan display quickly identifies the location of internal attachment welds and can be included in an inspection report.
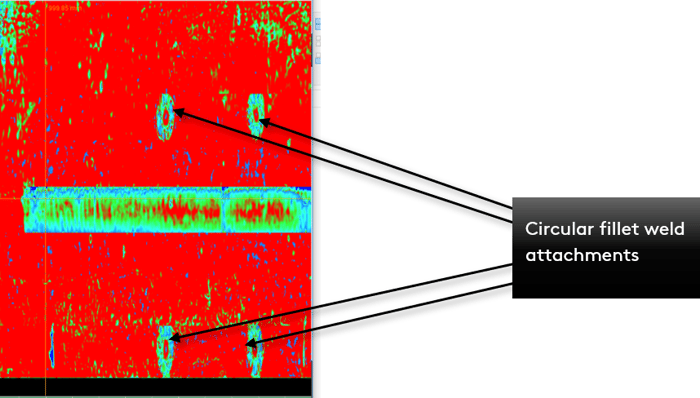
Eddyfi Technologies offers an advanced solution for detailed inspection of online and offline pressure vessels with the RMS PA phased array corrosion mapping system. Contact our friendly and knowledgeable staff to learn more about the better and faster solution for your pressure vessel, storage tank and boiler inspections now!
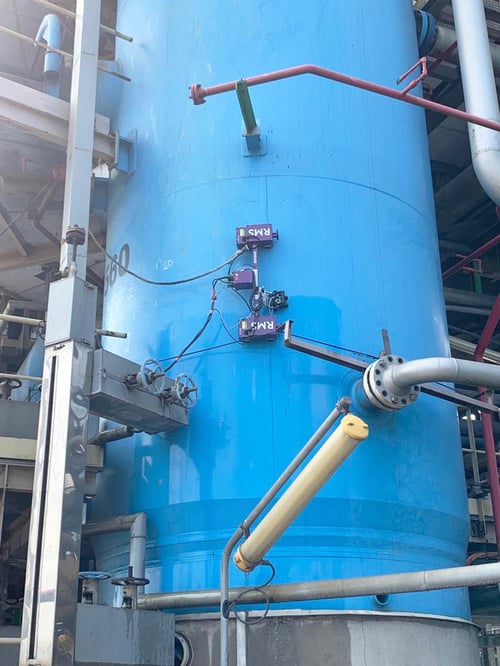