Storage tanks commonly found in the oil, gas, and petrochemical sector are typically constructed from welded steel plates. Although the main failure point in storage tanks is corrosion in the floor plates, the inspection of welds for defects is also critical and mandatory. Detection of through-wall defects at the welds is normally carried out using vacuum box technology, although this can be difficult to deploy at complicated lap welds or near obstructions. The traditional technology for inspecting welds for non-through-wall defects is magnetic particle inspection (MPI). MPI is said to work through coatings, but in reality, extensive surface cleaning and removal of any protective epoxy coating is required to provide any reliable results… When considering post inspection cleaning and re-coating, MPI ends up being quite expensive and time consuming.
Fortunately, there is a fast, cost effective, and well-established solution that provides high Probability of Detection (PoD) and rich information on crack length and depth. We present the Beyond Current solution.
The Alternating Current Field Measurement, or ACFM®, technique was specifically developed to detect and size surface-breaking defects on and around rough welds through several millimeters of non-conductive coating. This is a key advantage because just the costs associated with paint removal, post MPI re-blasting, and recoating is typically four or five times more expensive than the MPI itself. The benefits don’t end there; read on for more details!
While the main failure point in storage tanks is corrosion in the floor plates, from either the top surface or from the underside, the welded sections are also a direct source for damage mechanisms. ACFM is proving itself as the most cost efficient and trusted method for inspecting storage tank welds to supplement corrosion mapping, successfully detecting large cracks often missed by MPI. You can’t deny the cost savings of ACFM over MPI; overall, ACFM jobs are typically six times less expensive than their MPI counterparts while providing the added value of a more reliable inspection with data rich information to pass along to the asset owner.
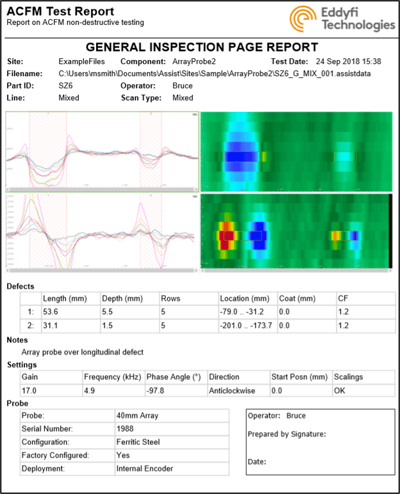
Tank floor weld inspection can be carried out using standard, general purpose, single sensor probes or inspection can be sped up using advanced multi-sensor array probes. Standard weld or pencil probes can be used to assess all anticipated geometries, but inspection speeds are relatively slow compared with their array counterparts. Compared to MPI, standard ACFM inspection with pencil probes is approximately 25% faster and 20% cheaper. But let’s not just note the savings here. If we consider the inspection of both the external and internal floor-to-shell filet welds of a 60-meter (200-foot) storage tank, the fees with MPI for blasting, inspecting, re-blasting and recoating have a median international cost of around $15,000 USD. The same inspection performed using pencil ACFM probes costs around $2,500 USD. While the MPI takes around four to six days for the necessary preparation and post-inspection work, standard ACFM is typically done in a day. All that is achieved while providing better PoD, depth sizing and auditable records.
No matter how you look at it the use of ACFM is a no brainer, even when considering it at its most basic form (pencil probes):
- You can do around five tanks by the time you would have done one with MPI
- For the inspection of five tanks (just the external and internal floor to shell welds), you would typically save $62,500 USD
- But ACFM has even more to offer… See below.
ACFM cost and productivity advantages can be further increased by using new and more advanced array probes for the filet weld. These new probes include a clever new way to estimate crack lengths that improve analysis speed and do not use moving parts.
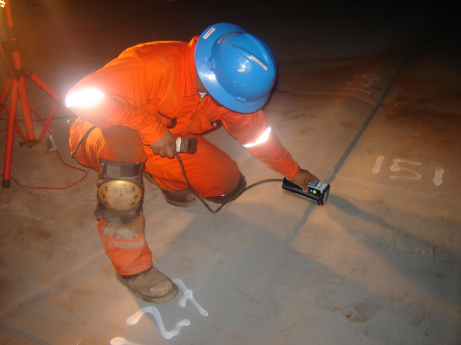
Floor and shell joints including lap joints can be assessed using the new high speed ACFM array probe which can further cut costs compared to MPI. With these new Sensu 2 ACFM® Compliant Array Probes, the overall inspection process is at least five times faster compared to any previous ACFM probes. While retaining all the advantages of ACFM, these probes also feature increased crack detection and sizing performance using ‘’Micro’’ sensors instead of the usual ‘’Mini’’ sensors. The array probe can scan areas up to 90 millimeters (3.5 inches) wide, utilizing twin-field technology for biaxial crack detection and sizing with up to 16 individually sprung ACFM sensors.
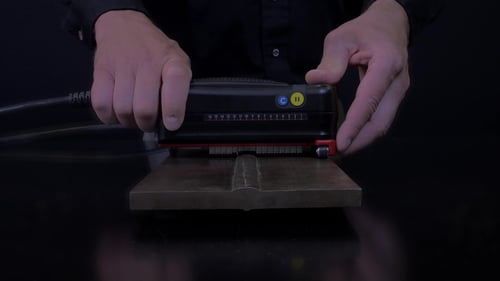
This is less fatiguing on operators which translates into highly productive, more reliable inspections. The array probe also has an embedded position encoder to automatically record defect locations and regulate data collection. In a single pass scan, a clear view of the weld cap, toes and HAZ is provided with rich information, including crack length and depth.
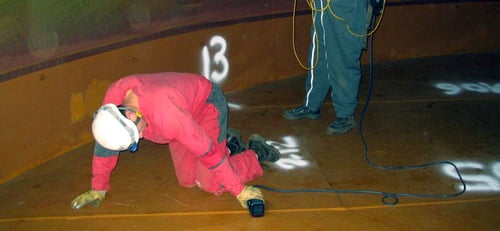
Paired with the TSC Amigo® 2 instrument, ACFM inspections enable rapid scanning with the handheld probe, reliable crack detection and characterization, reduced cleaning requirements, and a digital record of data for backup, offline and audit purposes. Weld integrity is at the heart of the role that efficient storage tanks play; a new generation of true ACFM technology offers the advanced NDT solution to provide the most comprehensive data to make informed decisions for proactive maintenance activities.
Alternating Current Field Measurement has received approval from several organizations including DNV, Bureau Veritas, Lloyds Register and ABS. Standard practice guidelines covering ACFM have been issued by ASTM (E2261/E2261M-17), ASME V and COFREND. Training schemes are available under CSWIP, PCN, and ASNT.
We invite you to contact us to learn more about optimizing your storage tank inspections today!