Right now, Eddy Current Array (ECA), Phased Array Ultrasonic Testing (PAUT), and other methods such as Alternating Current Field Measurement (ACFM) are becoming more advanced at accelerating rates. You can bet that in the next five to ten years there will be new contenders emerging in the NDT world, but here I’ll focus on the two most commonly available and affordable advanced methods used for gear inspection: ECA and PAUT.
Why ECA over PAUT for Gear Inspection
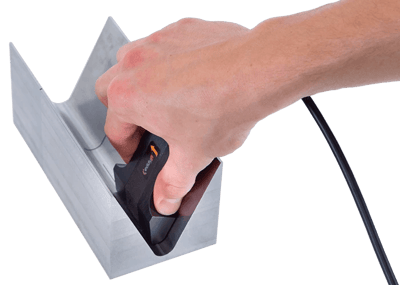
First, gear tooth failure is typically caused by surface-initiated fatigue cracking and other tooth surface conditions. This is what makes eddy current array my top choice for gear tooth inspection. It’s highly sensitive to surface flaws and is a “no-contact” method. No contact in this case means that no physical contact with the tooth surface is required to detect cracks; the practical upshot of which is that gear cleaning is not required. Combine that with the “J-probe” design made specifically for the contour of gear teeth and the advanced data imaging software that generates easy to interpret C-scan and isometric views, and you have the highest probability of detection available all within a very reasonable price range.
Second, these gears are made to be turning so they can make money. Having to scan your gear for cracks costs thousands of dollars per hour in production losses alone. So clearly, time is a factor. Even if you can align your inspections with other work, there are always tie ups and delays so in the end you want to be able to get the job done as quickly as possible with as little interruption to production time as possible. Once again, eddy current array takes the lead. Thanks to the probe design, ECA scans the addendum, dedendum, and root of the tooth in a single pass. This means that the entire tooth surface can be scanned in two passes: one on the active flank, and one on the non-active flank. In fact, the root gets scanned twice with this procedure.
Unlike with ECA, there is no official inspection standard for performing phased array on gear teeth. It is up to the technician to decide many of the correct variables suitable for each inspection, which opens the inspection up to a higher degree of human error and possible inconsistency of inspection quality from tooth to tooth.
The third major factor in deciding between ECA and PAUT is the condition of the gear teeth. Knowing the general condition of the gear teeth prior to hiring an inspection company is probably not what you would expect me to add in this list but hear me out. Eddy current array is very sensitive to surface defects and phased array is very sensitive to internal defects. So, if your gear teeth have progressive macro pitting to the point that crack indications may not be resolvable from the pitting indications you may not want to use eddy current array simply because it’s probably not going to tell you anything you don’t already know. In this case, phased array might be a better choice allowing the focus of the inspection to be on finding deeper flaws. Alternatively, you may have a gear that is in near pristine condition or only has minor to moderate surface flaws. In this case, ECA is the better choice because of its ability to render so much more information about the surface such as pitting patterns, wear patterns, indications of gear alignment issues, lubrication issues, as well as the detection of surface breaking cracks.
The fourth factor to consider is the stage at which the gear is in its life cycle. This is different from the tooth condition. When a gear is manufactured, they inspect the blank for flaws before the teeth are even cut. This inspection is often done with conventional or phased array ultrasonic testing. Eventually the gear sections must be shipped to a mill construction site and installed on a grinding mill or some other equipment. At this stage, just before installing the gear and putting the gear into service, I would recommend phased array and a surface method such as ECA or MPI (Magnetic Particle Inspection) be done as a baseline inspection of the gear teeth. At this stage it is also a good opportunity to ensure that the gear teeth are properly numbered on every fifth or tenth tooth. After the gear is put into service, it should be inspected with eddy current array every 12 or 24 months depending on the production risk of the asset in question. It is a good idea to increase inspection frequency if cracks are being found. It is suggested by major insurers and risk analysis engineers that an inspection be performed at least every six months for gears with known cracking.
At the end of the day, reliability engineers must look at the information provided by an inspection report and make decisions about their gears and the landslide winner in customer satisfaction in my experience is ECA. The reason for this divide, I believe, is due to the fact that the ECA inspection always includes a visual reference of indications observed in scans and because the report includes a complete list of inspection results for each scan. While with phased array, many internal discontinuities can be found in gear teeth that may never represent a serious threat to operation and can often not be mitigated due to their sub-surface nature. It is important to keep in mind that the power of ECA is more of a tool to narrow the focus of the visual inspection of the gear teeth rather than completely replace it and that when verifying crack indications; MPI and LPI are still the best tools for the job.
Given MTS’s inspection needs, technical specifications, practical demands, and safety concerns, Eddyfi Technologies’ plug-and-play ECA system was implemented as an integral part of our business for the following reasons.
Probe Design/Crack Sensitivity
As a standard, any ECA equipment that we chose would be required to detect a crack at least as small as 5 millimeters. The Reddy system easily achieves this, and Eddyfi Technologies has designed what I can only describe as the “gold standard” of gear probes.
Durability
We’ve already mentioned the inhospitable work environments of our inspections. The equipment must also survive grueling logistics and international travel. Keep in mind that (to my knowledge) the Reddy is the first fully self-contained, non-modular ECA unit with a fully functional touch screen display. In the past, setting up ECA systems onsite often required peripherals and unnecessary assembly that would introduce safety and ergonomic concerns for both the equipment and the operator as compared to Eddyfi’s easy and safe plug-and-play solution.
Reliability
Before adopting their systems, I visited Eddyfi Technologies to learn about their line of new ECA instruments. At the time I was used to another brand and skeptical about the “new kid on the block”, Eddyfi. But when they placed an Ectane 2 in front of me on the boardroom table, I noticed something about it that immediately gave me a good feeling. It was silent. Unlike the units I had become so used to over the years, there was no obnoxious fan noise or hollow droning. The density and compactness were audible. I could literally hear the quality of the instrument’s design. This was a better machine than I was used to, and I knew instantly that Eddyfi was on a warpath to win over customers like me.
And then there was the drop test and water hose videos of the Reddy… I was sold. With a new sense of confidence, my initial field test with the equipment would come shortly and that brings me to the final point.
|
|
Intuitive Software/Customer Support
The Reddy could not have been given a more appropriate name; it really is ‘Reddy’ to go in just minutes out of the box. I think that Eddyfi Technologies really hit the nail on the head with the Reddy’s software interface and desktop version of Magnifi. The tools that the Reddy offers in the field and ported to the desktop platform are precisely what is needed for the application of gear inspections. When we find crack indications on gear teeth, there are typically millions of dollars at stake. The software tools available in the field can be one of the factors that allow us to make the right decisions quickly. Thanks to a continuously evolving software development cycle and through their channels of customer feedback and one-on-one customer support, Eddyfi Technologies has been able to finetune their interface for added ease of use of important features and tools.
In conclusion, the Reddy is my top pick for ECA in the field. The development of the Reddy seems to have singlehandedly put the power of ECA solutions in the hands of just about anyone, anywhere… with a level of confidence that in the past would not have been possible. I hope that reading this has been informative and helpful. Check out my complete article on the comparison of ECA and PAUT for gear teeth inspection here, and please be reminded that this article is specific to gear teeth inspection which is not at all the same beast as weld inspection (where phased array really dominates the field). To learn more about Malenfant Technical Services, visit our website at https://malenfantindustrial.com.
And for Eddyfi Technologies’ blog readers interested in learning more about our product offering, get in touch here!