When it comes to ensuring the integrity of in-service pipelines and distribution systems, you need to make sure you have the tool that can deliver reliable inspection results under an array of conditions including extreme temperatures. It’s natural to associate extreme temperature with high temperature (like this pipeline operating at 350° C/662° F), but this article focuses on the other end of the spectrum. We look at the unique challenges of inspecting pipelines at cooler temperatures and present the Beyond Current solution.
Some pipework is more susceptible to failure from external factors like weather as cooler temperatures can facilitate particular damage mechanisms. According to the Pipeline Hazardous Material Safety Administration (PHMSA)1, nearly 6% of all distribution pipeline leaks in 2010 and 2011 were caused by natural forces, as shown in Figure 1. Cast iron pipe, unknown material pipe, and steel pipelines installed before 1950 appear to have a higher failure rate when exposed to cold weather.
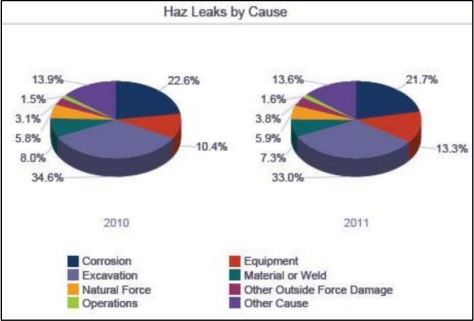
Figure 1: Source of Distribution Pipeline Failure1
In-service pipelines operating at these extremes are vulnerable to a range of circumstances that can cause excessive stress or strain leading to pipeline component failure. Loads on pipelines from ice and snow build-up, erosion from ice and snow melts, and thermal stresses due to temperature extremes are all factors with frost heave being responsible for most cold weather-related failures. Displacement of ground surface or pavement is a hint of frost heave impacting buried pipes. The earth movement creates excessive longitudinal stress that can further promote pipeline failure when circumferential stress corrosion cracking, low-quality threaded connections or girth welds are also present.
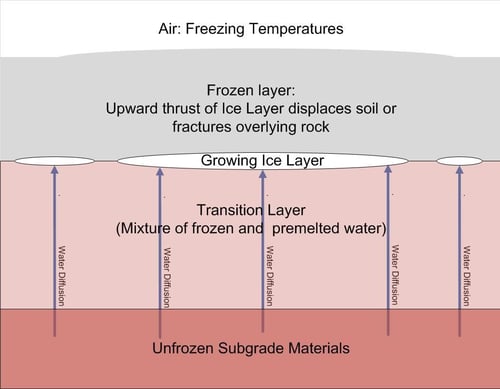
Figure 2: The Evolution of Frost Heave
While cold weather has been reported as affecting both buried and above-ground installations, the actual pipe contents itself can also create a volatile environment for integrity threats. Consider LNG liquefaction plants with pipework containing propylene and ethylene, hydrocarbons often used as refrigerants. Inspecting pipelines operating at extremely low temperatures really isn’t an option for many NDT techniques.
So, when a Middle Eastern plant had a requirement to identify areas of metal loss on various refrigerated propylene and ethylene pipelines ranging between 3- and 24-inch (76- and 610-millimeter) diameters, they turned to Eddyfi Technologies for a solution: the proven Sonyks™, formerly known as the Teletest Focus+, guided wave ultrasonic testing (GWUT or GWT) pipeline inspection tool.
All the pipelines were at elevated heights so guided wave testing was the ideal technique as 100% of the pipeline could be inspected with the pipe only requiring direct access at localized scaffolding. This reduced inspection costs for the end client and increased productivity.
Operating at more than -50° C (-122° F) combined with the pipeline humidity, ice developed quickly at the surface of the tool location once the insulation had been removed. Due to the rapid data collection ability of the Eddyfi Technologies long-range UT (LRUT) system, the test sequence could be collected and completed before excessive icing of the pipeline and tooling occurred.
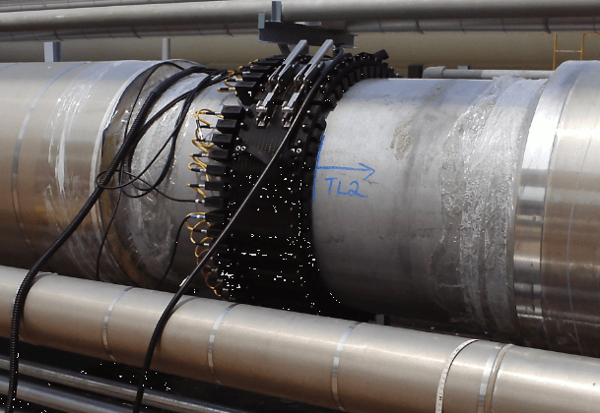
Figure 3: Typical Tool Location
As seen in Figure 4, excellent Signal-to-Noise Ratios (SNR) were achieved on these low temperature pipelines with the extreme operating temperature having little or no effect on the data quality.
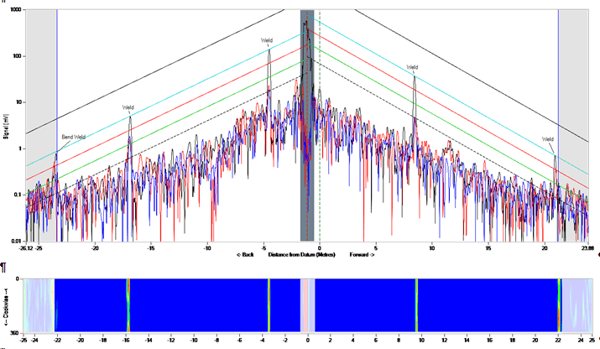
Figure 4: A-Scan and A Map
For more information on how the Sonyks guided wave testing solution can help you keep your cool when monitoring integrity threats due to cold temperatures (or hot, and many other extremes), contact one of our NDT experts today.
1www.phmsa.dot.gov