People often think that assets built using austenitic stainless steel (SS) are protected from corrosion in all situations. Although the thin layer of chromium oxide covering the SS protects the components in wet or humid environments, an environment with higher chloride content puts the asset at risk for corrosion and other damage. Where can we find such an environment? Consider offshore or near shore installations where ambient air has a higher concentration of chloride coming from the seawater. Or again, let’s think of chemical and petrochemical plants, or even water pipes and other structures found in the food and beverage industry. Even poolside accessories are susceptible to Chloride Stress Corrosion Cracking (CSCC)!
Alternative materials like ferritic-austenitic SS or duplex or added protective coatings (Thermal Spray Aluminum or TSA) are now in use where chloride content is considered a potential threat, but multiple assets were built without it and need to be regularly inspected in order to verify their integrity and repair or replace them if needed. More importantly, any piping or vessel that has been built and put in service prior to the 1970s is at greater risk as the purity of the alloy was less controlled during that time.
Let’s see how CSCC develops and what our options are to detect it before it’s too late…
As mentioned, stainless steel is resistant to corrosion in wet or humid environments thanks to a thin layer of chromium oxide that covers the material. On the other hand, this oxide protection remains susceptible to chloride attacks. Think about a component that is in direct contact with a liquid containing a high concentration of chloride, although ambient air can also be the cause for chloride corrosion. Chloride ions evaporate from sea water and can deposit on the stainless steel. In the beginning, the amount is small enough that it won’t cause any damage but over time there is an accumulation of chloride ions on the surface, and at some point, pitting or crevices will start to form.
The pits or crevices may continue to evolve as corrosion, but in environments where the temperature increases (≥ 60° C or 140° F) and residual stress or other mechanical constraints exist in the material, cracks can start to form and will evolve faster than corrosion.
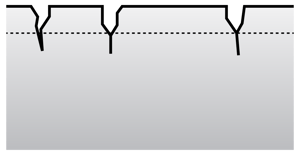
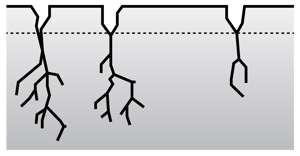
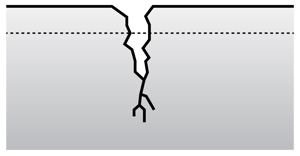
Left to Right: SCC or Fatigue Cracks Nucleate at Pits, SCC Cracks are Highly Branched, Corrosion Fatigue Cracks have Little Branching
Using an NDT technique to detect pits allows further action to avoid the pits from progressing through wall and causing a leak or evolving into CSCC which could lead to pipe or vessel break. One can easily imagine that failure of a vessel or pipe could put the safety of workers at risk or lead to the release of hazardous chemicals in the environment. Such event would impact the integrity of the plant and incur loss of performance and costs for repair. In addition, these disastrous events could potentially have a huge impact on the environment and on the population’s health.
There are different NDT methods that can be used to achieve detection of the pits or cracks. Visual inspection, penetrant testing, ultrasonic testing, and eddy current array are discussed here.
One of the current techniques used is Visual Inspection (VI). This technique, despite having some advantages (cheap, easy to deploy, no extensive training required) is not the best approach if used alone. The downsides of this technique are mostly the same as those of penetrant testing.
Penetrant Testing (PT) has very interesting advantages: it is cheap, sensitive to small pits, and doesn’t require a lot of training. On the other hand, the surface under inspection needs to be visually accessible and must be thoroughly cleaned for the chemicals to perform as expected. The human factor is very important and is not something we can control well. The lighting, visual access, and operator’s eye health are just some of the factors we cannot control but that have a major impact on the output of an inspection. Moreover, depending on the inspection conditions, the technique itself can underperform (e.g. if there’s condensation on the pipe or if the cleaning hasn’t been done properly). Finally, the impact of using chemicals on the environment and on the inspector’s health shouldn’t be ignored.
As for Ultrasonic Testing (UT), this technique would be adopted mainly once the cracks/pits have evolved into bigger indications (ø ≥ 2mm or 0.08in for pits, or cracks deeper than 2-3mm or 0.08-0.12in) and ideally if they were on the far side. Moreover, the fabricated and welded austenitic stainless steel components are characterized by a bigger grain structure than ferritic SS causing high sound attenuation and to some extent, false signals. This factor isn’t a complete no-go, but detailed and adapted procedures and highly trained operators would be necessary to conduct successful inspections. Finally, geometry and the presence of welds can also complicate UT inspection: multiple probes, complementary scans, and some limitations with crack orientations in some areas, etc. are to be taken under consideration. On the other hand, one of the benefits of UT is its capability to perform depth sizing, which would make it a great complement to the following technique, Eddy Current Array (ECA).
Eddy current testing is a surface inspection technique, meaning that it has a limited depth of penetration. In applications where the flaws are subsurface or located on the far side of the component, ECA can be more limited. But when looking for CSCC, which starts with tiny open surface pits, ECA is an excellent solution. Basically, anything that is currently inspected with PT can also be inspected with ECA, but with the advantages of being faster (reduced surface preparation, no dwelling time, high scan speed, wide coverage, etc.), digital (data saving and archiving capabilities, encoded scans, software processing tools, etc.) and has a much lower operator dependency. ECA can detect and differentiate both the pits and cracks.
Recent trials and studies on various machined and natural samples have demonstrated that ECA offers great performance to detect CSCC in its early stage. CSCC is commonly found on pipes of various diameters so to ease the inspection and get a uniform response, the Manual Pipe Scanner (AMPS) and I-Flex probes are the tool of choice to perform these inspections. The directionality of the I-Flex probe used in Transmit-Receive mode also easily provides information on the flaw type (volumetric or crack like) and on its orientation, in the case of linear indications.
The following images illustrate the tooling used and results coming from a 60mm or 2.4in tube that suffered from CSCC.
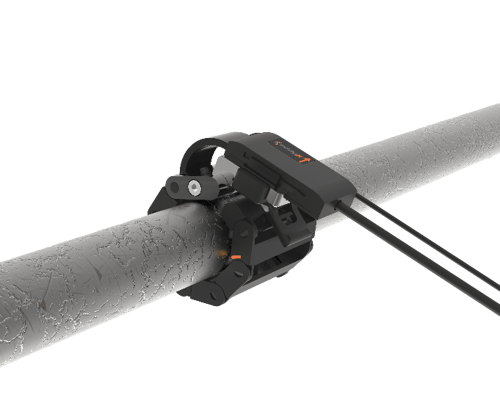
The I-Flex and AMPS can adapt to pipes and tube ranging from 38.1 to 150mm or 1.5 to 6in in diameter. Large pipes (6in/150mm and up) can be inspected using the Spyne™ array probe tool.
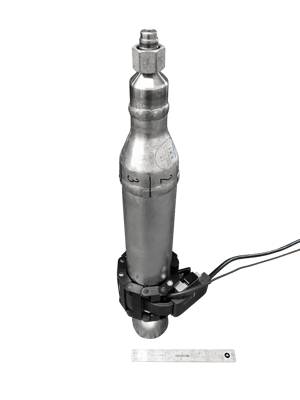
The above system is shown installed on one of the test pieces –SS304- with natural CSCC. Considering the pit size, the small I-Flex probe with 2mm/0.8in coils was selected. A total of six passes were required to cover the full circumference of the sample (Note: Custom probes can be designed for different geometries or to increase coverage).
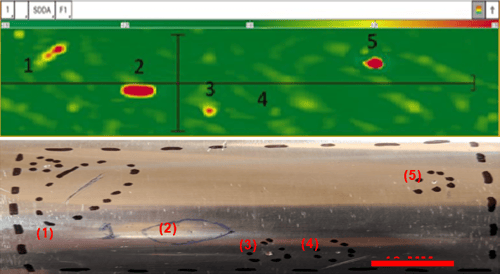
Small area of the above sample with five indications
Blind tests were also conducted by two different parties using Eddyfi systems on a set of five manufactured and real samples. Both parties obtained the highest score of the trial by using the I-Flex probes and AMPS in combination with advanced software, Magnifi®. During this trial, a manufactured sample was also put to test and confirmed the detection capability on pits as small as 0.5mm or 0.02in in diameter by 1mm or 0.04in deep. Surface finish, coating thickness and geometry/probe fit can affect the minimum detectable flaw size, but nonetheless, the results achieved are very impressive.
With ECA being a volumetric detection technique, depth sizing is limited but qualitative estimations are possible, or once the large area is scanned with ECA, complementing it with UT in the areas of interest will provide fast and accurate results. The benefits of deploying ECA to detect CSCC are considerable and could save time, money and even lives.
If you’re interested in learning more about eddy current array for early detection of chloride stress corrosion cracking in stainless steel components, we invite you to contact one of our NDT experts today and stay Beyond Current.