Non-ferromagnetic heat exchanger tubes (e.g., INCONEL®) are prone to circumferential cracking. Most circumferential cracks are located adjacent to support structures or expansion transitions (tubesheet), both generating important signals, masking the small crack signals when inspected with conventional eddy current testing (ECT).
The non-ferromagnetic alloys used to make heat exchanger tubes are, as you might expect, non-conductive and offer a better resistance to corrosion and stress-corrosion cracking (SCC), which is necessary in the power generation and nuclear industries because of the critical nature of the systems they are part of.
Common heat exchanger components experiencing the problem of circumferential cracking include feedwater heaters and condensers at power plants, as well as heat exchangers in petrochemical refineries.
Circumferential cracking is very difficult to detect and characterize with standard eddy current bobbin probes, still the norm in the industry to inspect non-ferromagnetic alloy tubes, because:
- These probes are very sensitive to tube expansions and ferromagnetic alloys, which tubesheets are usually made of. Because circumferential cracking is usually in the vicinity of the tubesheet, it becomes very difficult to isolate the signal generated by small-volume cracks from the complex signal composed of cracks, geometry changes, added material, and the noise from the tubesheet.
- The design of conventional ECT bobbin probes positions coils in such a way that eddy currents flow parallel to circumferential cracks, making them virtually invisible to the technique.
Heat exchanger owners, of course, want to identify tubes leaking from circumferential cracking, but they are usually more interested in identifying tubes showing signs of cracks that could grow to 100% through wall while the heat exchanger is in service. Traditionally, the power generation and nuclear industries inspect tubes with ECT probes because the technique is perfectly suited to inspecting these non-ferromagnetic alloys, sometimes using IRIS testing or rotating pancake coil (RPC) probes as a secondary verification method.
Inspection Technology Detection Capabilities According to Defect Type
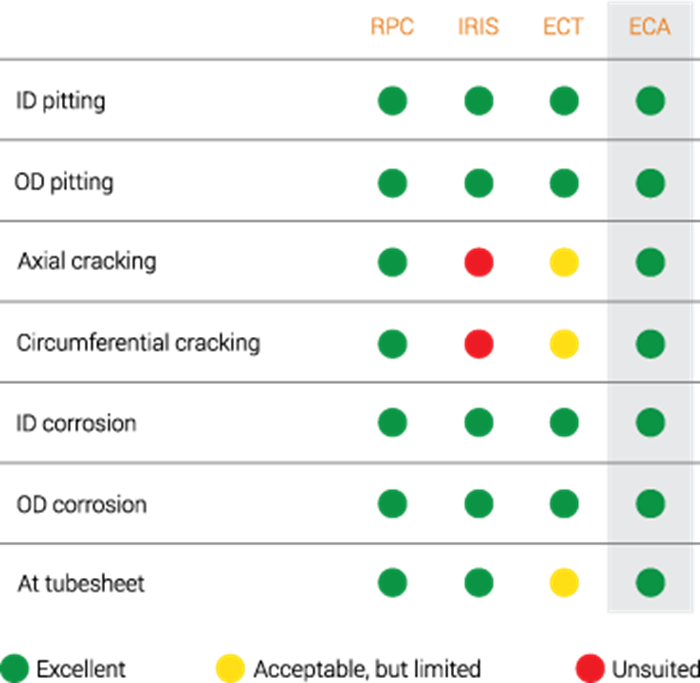
Inspection Technology Sizing Capabilities According to Defect Type
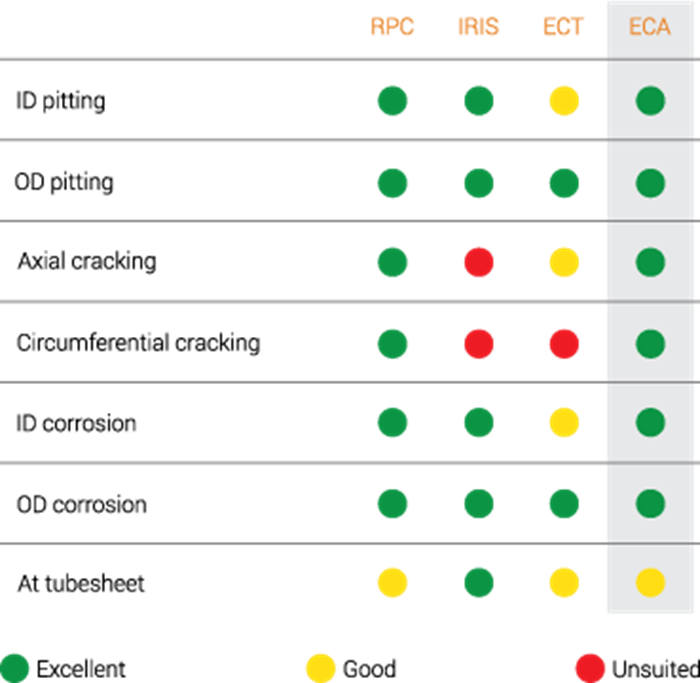
RPC probes have been around for decades. They were developed in the 90s to detect SCC and are still common today. They use a motor that makes the coils turn in a helical pattern inside the tube. The surface-riding pancake coils scan inside tubes looking for defects such as small circumferential cracks that usually elude bobbin probes. RPC probes are precise, as they’ve demonstrated time and again, but because of the heavy strain placed on RPCs, the motor and probes must be replaced quite regularly.
However, RPCs are also quite slow. Typical inspection speeds are well below 25 mm/s (1 in/s) for RPC probes, 12 mm/s (0.5 in/s) being fairly normal, making inspections with RPCs quite time consuming. This relegates the technique to inspecting the tubesheet area and serve as a backup to conventional bobbin probes for short tubing sections.
Eddy Current Array Technology
ECA technology groups several individual coils inside a probe, where they are excited in such a way as to eliminate the interference from mutual inductance between them. This is a process referred to as multiplexing, which enables the coils to work together to thoroughly sweep the interior surface of each tube.
The ingenious coil configuration in an ECA tubing probe such as Eddyfi’s DefHi probe allows eddy currents to flow perpendicular to circumferential defects, making them much easier to isolate and characterize. Further, optimizing the distance between transmitter and receiver coils to make the expansion signal flat compared to other signals makes the signal easy to filter out.
The transmitter-receiver mode of the coils yields an absolute signal response with phase and amplitude information, also something very useful when it’s time to characterize defects.
ECA tubing probes can also be designed to strike a balance between an optimal frequency for the non-ferromagnetic material under test and generating clearly distinct tubesheet and circumferential cracking signals. Thanks to multiplexing, the probe generates data that helps operators estimate the circumferential length and the position of defects, which is impossible with a bobbin probe.
Using analysis software like Magnifi makes using the additional data from the ECA probe to display C-scans possible. Because tubesheets generate an angular signal in relation to circumferential defects, their circumferential length and depth are clearly visible in C-scans. By applying an appropriate high-pass filter on the data, completely isolating defects has never been easier.
Data from ECA Tubing Probe
Individual array coils in an ECA tubing probe provide phase data on top of amplitude information. The phase component can be rotated in C-scans to get a defect response of the highest possible definition. Under real-world testing conditions, ECA probes were capable of detecting and sizing circumferential cracks at the tubesheet as early as 50 % wall loss and 30 % in the free span area.
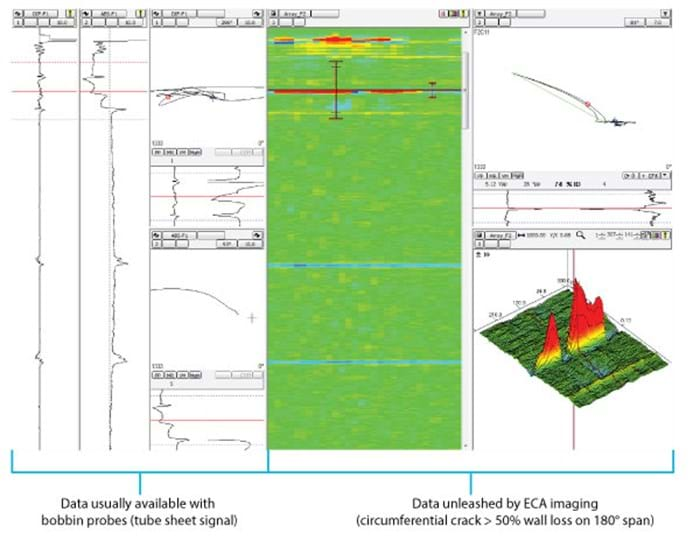
When it comes to inspection speeds, ECA depends on the number of channels, the size of tubes you’re inspecting, and the lowest frequency of your configuration. The lower the frequency, the longer it takes to perform acquisitions during each multiplexed timeslot. Thin walls and low conductivity, however, make for fast inspections because, in this case, the lowest frequency is still quite high.
For example, typical inspection speeds would be:
- Stainless steel tube with a 19.1 mm (3/4 in) OD: 350–750 mm/s (14–30 in/s)
- Brass tube with a 19.1 mm (3/4 in) OD: 250–400 mm/s (10–16 in/s)
- Stainless steel tube with a 25.4 mm (1 in) OD: 350–520 mm/s (14–21 in/s)
- Brass tube with a 25.4 mm (1 in) OD: 200–300 mm/s (8–12 in/s)
Therefore in most cases, ECA inspection speeds are at least 10 times greater than RPC probes with data quality similar to RPC probes.
The Takeaway
When we compare ECA tubing probes to ECT bobbin probes, ECA probes enable differentiating the various complex geometries inside non-ferromagnetic alloy heat exchangers, enabling accurately detecting, sizing, and characterizing small-volume circumferential cracks.
Compared to RPC probes, which usually scans tube ends at approximately 40 seconds per tube, ECA probes can scan tube ends at 5 seconds per tube. Being less sensitive to pull speed, ECA probes also don’t need a probe pushing device to accurately control the axial speed.
Other advantages of ECA tubing probes like the DefHi probe include:
- Quantifying the circumferential extent of crack defects
- Accurately locating and characterizing crack defects in the vicinity of the roll transition
- Unlike rotating probes, the solution can be used for full-length tube examinations
- C-scans give personnel without extensive eddy current testing data analysis experience the necessary confidence about their inspection results
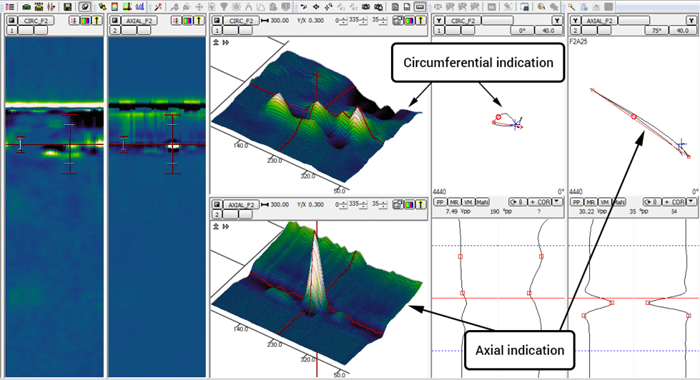