Hard spots may be the result of a deviation from uniform quenching procedures during pipeline build, although a more prevalent manufacturing defect prior to 1970. The sustained stress of the pipeline’s internal operating pressure combined with the increased brittleness from any hard spots present with mechanical damage provide the perfect recipe for failure. Hydrogen is a common reaction to the cathodic protection commonly found in pipelines, and its presence makes hard spots susceptible to hydrogen induced cracking, or HIC. Stress Corrosion Cracking, or SCC, is another type of cracking that can lead to pipeline failure should it reach a hard spot. We are all aware of the consequences of cracking found inside hard spots.
So, how do we “spot” these pipe wall metallurgical anomalies? Initial screening with in-line inspection, or ILI, tools employing magnetic flux leakage or eddy current based technologies will identify areas with greater metallurgical hardness along the pipeline. Direct assessment by way of integrity digs accommodate further investigation to more accurately assess the hard spots found. Nital etching has been used to detect surface variations related to hard spots. Also known as temper etch or surface temper etch, this method highlights softer tempered areas by burning and therefore darkening them faster than harder regions. In order to be effective, nital etching requires intensive surface preparation – to the point of almost being polished. Given the long process, technicians will focus solely on the regions with indications from the ILI tool. To compensate for potential position offsets, they’ll need to examine larger areas. This selective follow-up puts the pipeline at risk of being reburied with missed hard spots.
Enter the Spyne™ array probe. This adaptable surface eddy current array, or ECA, screening tool is the solution for better pipeline hard spot detection. Because of its very high sensitivity to magnetic and conductivity property changes in alloys, the eddy current technique has been well used by the industry for material sorting. This characteristic makes ECA the tool of choice for hard spot detection because significant microstructure changes that occur during localized quenching will strongly affect pipeline properties. This allows Spyne to easily detect 100% of the hard spots called by ILI tools and more so that no hard spot is left undetected.
But it doesn’t stop there. The cumbersome process involved with the usual magnetic particle inspection, or MPI, for SCC assessments can also be replaced by the more efficient Spyne solution. The ECA probe will scan for hard spots and simultaneously identify every type of linear breaking defect on the outer pipeline surface including stress corrosion cracking and hydrogen stress cracking, but also fatigue cracks, lack of fusion in electric resistance welded or A.O. Smith flash welding, and/or manufacturing flaws. Depending on the pipeline diameter, Spyne delivers a 360-degree map of hard spots and cracks along the full joint length within minutes – a significant improvement over nital etching and MPI. The highly repeatable measures afforded by this reliable plug-and-play tool means no interpretation required and a controlled human factor. Get better acquainted with this ECA solution with the Spyne ECA Product Training course.
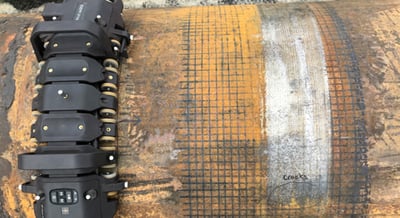
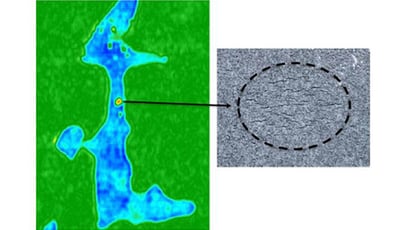
Pipeline integrity assessments are only as good as the equipment being used to reveal any weakness. Trust the Spyne to not take any chances. And when the pipeline inspection calls for corrosion mapping, turn to the proven Pipescan™ HD. Whatever way you look —from cracks to corrosion— we’ve got you covered! Contact our NDT experts to learn more about our full range of advanced NDT solutions for your pipeline inspections today!