In a previous article, we discussed Guided Wave Ultrasonic Testing (GWUT or GWT) for extremely small diameter pipelines. Today, we take a look at the other end of the spectrum thanks to our friends at Echo NDE who shared an example of inspecting LARGE diameter pipelines... and when we say large, you have to see it to believe it. Discover the Beyond Current solution that delivers reliable data fast for better informed decisions.
Those of us who have been or are still actively involved with guided wave inspections probably have a clear memory of their first inspection. I know I do. My first self-led guided wave inspection was deep in the Amazon. I can remember feeling nervous before the trip; the pipeline in question had known issues so it was important that I went over there and did a good job. The inspection went very well and became an excellent foundation for me to build upon. I learnt a lot on that job. I still remember the length of my longest guided wave shot, and I can recall some of the more 'unusual applications' where I have been involved.
I also have clear memories of the largest diameter pipes I have tested; there have been some sizable pipes during my time as a guided wave inspector. I inspected a 48-inch (1.2-meter) diameter flare line in Sicily and a 54-inch (1.4-meter) pipeline in Mexico, to mention only a few.
Social media has had a significant effect on the way we are now able to interact with our customers. In the past, if we were lucky, a client would occasionally reach out to us to share a story of a recent inspection, or maybe to ask for advice on a future one. Today, thanks to social media, these interactions are commonplace. It's fantastic to see Eddyfi Technologies customers posting videos and images of their products in action in real-world scenarios.
I was recently scrolling through LinkedIn and came across a post from Echo NDE, a Canadian-based client who had taken the inspection of large diameter pipelines to another level: They had successfully completed a guided wave inspection of a buried 72-inch (1.8-meter) pipeline! A special thanks to Jeff and Ed for taking the time to provide us with details of the job.
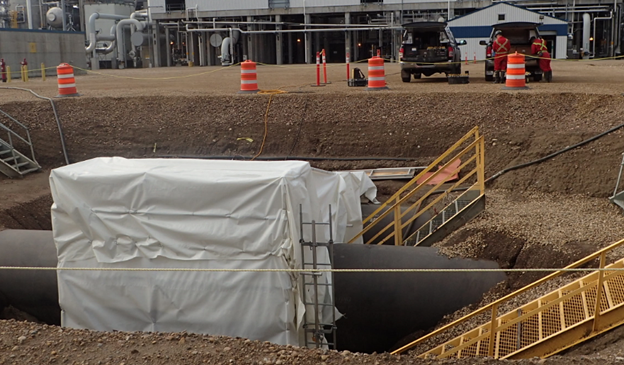
72in/1.8m Buried Pipeline - Image courtesy of Echo NDE
Inspecting a pipeline that's large enough for most people to walk through is not an easy task. Due to its size, most methods of NDT would not be an option in the first place. This scenario was even more difficult as the pipeline was not only buried but also featured both internal and external coatings. The list of applicable non-destructive methods becomes very small. As users of the Teletest Focus+™ guided wave pipeline inspection system for many years now, Echo NDE were equipped with the ideal solution to their client's problem. Although, a solution for this scenario —a 72-inch (1.8-meter) pipe— is not your standard guided wave inspection.
For this application, three separate Teletest collars needed to be linked together to construct a bracelet tool to fit the extreme pipe diameter. This task is physically more demanding and time-consuming than a normal guided wave inspection. Echo NDE used a three-person team to ensure that they were safely able to completely link all collars. A guided wave pipe inspection of this diameter is all about preparation, and in this case, taking the time to ensure that all three collars were fine-tuned to achieve optimized transducer coupling.
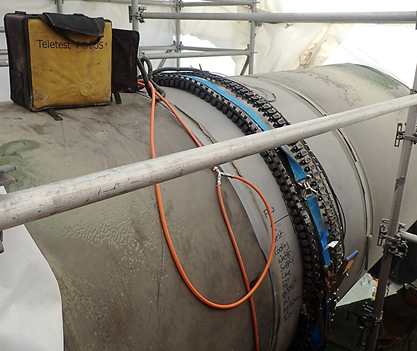
72in/1.8m Buried Pipeline Close Up - Image courtesy of Echo NDE
Once the extended collar was installed, data was collected relatively quickly. Echo NDE was pleased with the results and managed to inspect 124 feet (37.4 meters) of the pipeline. To put things in perspective, a 72-inch (1.8-meter) pipe has a circumference of around 18.7 feet (5.7 meters). That's around 220m2 of pipe inspected from a single test location, in less than half a shift — impressive productivity by any standards. The end client had concerns that the pipe may be subject to corrosion due to localized coating failure but on review of the data Echo NDE concluded that the inspected pipe section was in good condition with no concerning indications. By being prepared to inspect the very limits of the capabilities of their Focus+, Echo NDE was able to provide an efficient inspection solution for their end client.
This type of inspection reminds me that we can learn so much from our clients. They are the 'coalface' using our Teletest test instruments and so ideally placed to give meaningful feedback. This is vital in guiding our continuous improvements that help ensure our clients stay Beyond Current - tag us on social media showing us how you stay #BeyondCurrent. Not a proud Teletest Focus+™ equipment owner yet and interested in learning more? Contact our team of NDT experts to discuss the best inspection solution for your application today!