In this third and final installment of our inspection speed series, we’ll talk about the case of rotating probes vs. eddy current array probes.
RPC probes have been around for decades. They were developed in the 90s to detect stress-corrosion cracking (SCC) and they are still common today. They complement eddy current testing (ECT) probes when more precision is necessary. RPC probes use a motor to make them turn in a helical pattern inside tubes. As its name suggests, an RPC probe uses surface-riding pancake coils to scan inside tubes looking for defects that can elude ECT probes, such as small circumferential cracks. RPC probes have demonstrated time and again they are precise. They’re, however, somewhat fragile and have one major drawback: a low inspection speed.
RPC Probe Inspection Speed
It’s common to see inspection speeds of RPC probes under 25 mm/s (1 in/s), 12 mm/s (0.5 in/s) being fairly typical. Inspections involving rotating pancake coils probes are therefore very time consuming. This relegates them to the tubesheet area, acting as backup to conventional ECT for short sections of tubing.
On the other hand, you have eddy current array technology. It doesn’t rely on a small motor nor is it a slave to rotation speeds. It can therefore offer a better speed and perform single-pass inspections.
ECA tubing probes rely on an array of coils that’s multiplexed. This yields high-definition data very much like rotating pancake coils probes, without the inspection speed limitation.
With eddy current array probes, the inspection speed depends on the number of channels. This relates to the type of probe you’re using, the size of the tube you’re inspecting, and the lowest frequency of your configuration. The lower the frequency, the longer it takes to perform acquisitions during each multiplexed timeslot. Thin walls and low conductivity, however, still allow for fast inspections because the lowest frequency remains quite high.
For example, the typical inspection speed of the following tubes is:
- Stainless steel with an outer diameter (OD) of 19.1 mm (3/4 in): 350–750 mm/s (14–30 in/s)
- Brass with an OD of 19.1 mm (3/4 in): 250–400 mm/s (10–16 in/s)
- Stainless steel with an OD of 25.4 mm (1 in): 350–520 mm/s (14–21 in/s)
- Brass with an OD of 25.4 mm (1 in): 200–300 mm/s (8–12 in/s)
In most cases, this is at least 10 times faster than RPC probes.
Of course, this speed comparison is completely worthless if the quality of the data cannot be compared, too.
Look at the following scan data from a condenser tube.
You can see that a deep circumferential crack is detected. The results from the ECA probe clearly shows that the crack is circumferential because the the axial C-scan (bottom center) does not display a response signal.
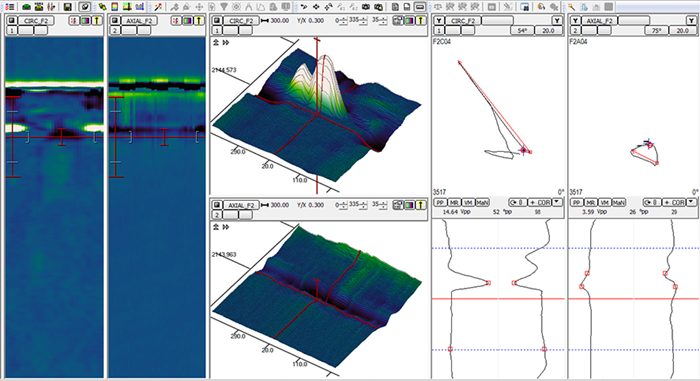
Here, not only does the ECA probe show the axial crack, but also a number of smaller circumferential cracks, that elude the RPC probe.
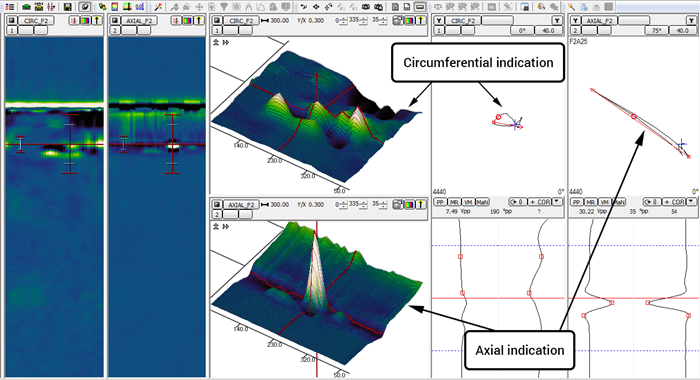
There you have it. It had to be demonstrated, but as you can see, ECA probes can yield the same levels of coverage and precision than RPC probes, at unmatched inspection speeds. Actual field use of ECA probes revealed that they can be successfully used in full-length tube examinations. Eddy current array tubing probes have detected defects at baffles that went previously undetected simply because RPC probes had only been used at the tubesheet… on account that it was too time consuming.
Take a look at our complete tubing probe lineup to see for yourself how they measure up or use our Tubing Probe Creator to find out just what probes suit your specific application.