Eddyfi Technologies has developed a phased array ultrasonic testing (PAUT) package for the inspection of axisymmetric parts welded by a laser or electron beam process. This package can be easily incorporated into a complete solution by integrators and end users. This article illustrates some applications of this package for the automotive industry with a transmission control gear and hybrid engine rotor inspection.
There are several gear and rotor parts within a car engine that are welded together using a laser or electron beam process. Cracks, lack of fusion, and lack of penetration are some of the defects that can occur during the welding process.
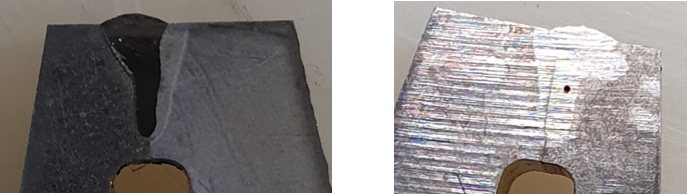
From an ultrasonic standpoint, there are inherent difficulties with the inspection such as restricted access, material (cast iron, for example), entry surface not parallel to the weld, some indications like porosities and welding recovery need not be classified as defects, cold cracks, and the list goes on.
While conventional UT solutions exist, Eddyfi Technologies has developed a PAUT solution that provides several advantages to customers:
- Higher productivity as the full volume of the weld is inspected with only one turn
- Less mechanical parts for full volume inspection equals less complexity for integrators
- Better flexibility to adapt to the geometry
- Smaller dead zone thanks to capability to deviate/focus beam electronically
- Reduced false alarm rate
- Flexible defect detection algorithms to better dissociate indications
- Inspection process monitoring
- Better traceability (log file, unitary part reference capability, statistical inspection results, etc.)
Gear Inspection
The inspection of axisymmetric parts is typically done in immersion by sending a beam radially into the weld seam using a fixed PAUT transducer and rotating the part. In response to accessibility issues, Eddyfi Technologies has developed various PAUT probes adapted to the different gears/rotors for inspection using simulation tools.
The PAUT system used for this automotive inspection application is the Multi2000 Pocket, a small and lightweight PAUT system in a rugged box. The system can adjust the beam focalization and scan the part geometry making it more adaptable to new parts compared to conventional UT inspections. The following image shows the position of the probe with respect to a differential gear.
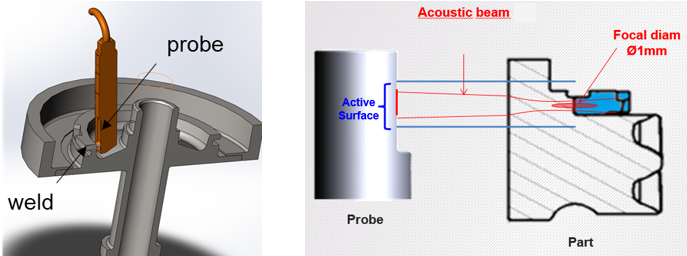
The inspection consists of a combination of electronic scanning and electronic focusing with electronic beam steering to ensure 100% coverage of the weld. Electronic steering is necessary to reach parts of the weld which would not otherwise be inspected using only a beam normal to the surface such as the one obtained with a conventional UT probe. Electronic focusing leads to a focal beam of less than 1 millimeter (0.04 inches) across the weld allowing for detection of small indications.
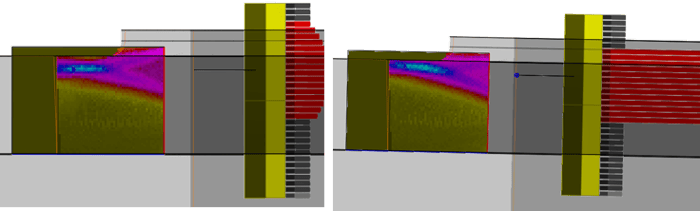
Weld coverage can be verified using parts with calibrated defects across the full length of the weld. The following image on the left shows a differential gear with various flat-bottomed holes (FBH) positioned in the middle, top, and bottom of the weld. The images on the right show the scans obtained for each of the FBH. The FBH are all detected without any difficulty guaranteeing full coverage of the weld.
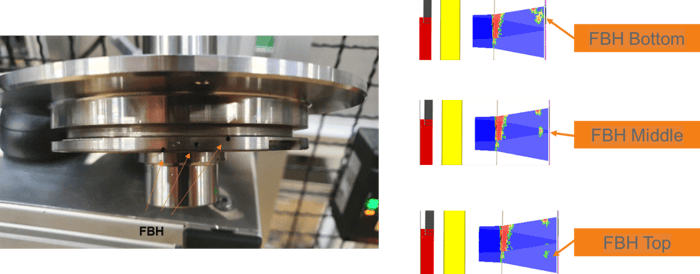
Rotor Inspection
This solution also applies to the inspection of rotors inside the electric part of a hybrid engine. The inspection uses a tandem pitch-catch solution with the same PAUT probe as the weld is vertical and access is limited to the top of the part. The image on the left shows a cross-section of the rotor with a superimposition of the configuration for one of the delay laws. A group of elements sends an acoustic wave with an angle that rebounds off the backwall. The receiving delay law is identical, but with a different group of elements it captures indications on the first leg. This configuration is traditionally used for the inspection of narrow bevel welds.
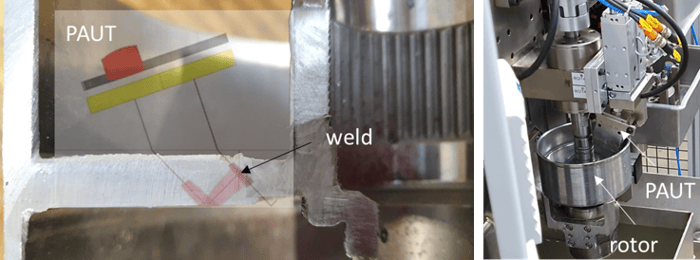
PI2K
Dedicated software for axisymmetric welded part inspection called PI2K was developed to handle the full inspection from data acquisition, communication with the programmable logic controller (PLC), data analysis, and process monitoring.
The main functionalities are:
- Simplified Graphic User Interface (GUI) for operators and supervisors
- Data configuration and acquisition
- Real time display for easier analysis/settings
- Communication with PLC (mechanical displacement synchronization, etc.)
- Process monitoring (coupling, probe position, rotation eccentricity, etc.)
- Independent weld depth monitoring and defect detection parameters
- Calculation of weld length (percentage of the circumference) and number of defects
- Verdict of inspection (good/not good) depending on editable criteria for each part type
- Calibration mode
- Traceability
The following image shows the GUI with the scan result obtained for the master part described before. In addition to the three FBH, this part contains four notches. The horizontal axis represents the rotation of the part and the vertical axis is the height of the weld. After calibration, the electronic scanning PAUT data is transformed into a red/color palette with a rejection criterion fully customizable based on the final automotive part inspection application.
The holes and notches are clearly visible and indicated in red. Filters can be applied to reject small indications and/or indications that are not considered as defects. Detection algorithms are then applied to measure the length and height of the indications.
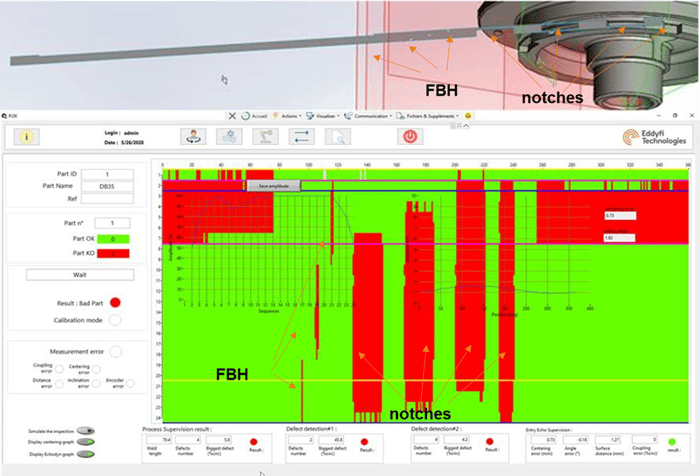
The result is saved together with the following sample information that can be used by the manager responsible for production quality:
- Date/Time
- Part type
- Weld length
- Mean weld height
- Weld height standard deviation
- Result of the control (number, size of defects)
- Percentage of uncoupled circumference
- Error of centering
- Error of inclination
- Number of defects
- Unitary part serial number (if provided by PLC)
The following videos show a rotor (top) and differential gear (bottom) inspection using the solution provided by Eddyfi Technologies.
If you are in the market for an axisymmetric welded part inspection solution, we propose a package with a PAUT system, probe, and data acquisition/analysis software installed on a compact PC that can be easily integrated with a complete mechanical solution. Our system is flexible and can be adapted to any axisymmetric parts welded by laser and electron beam welding.
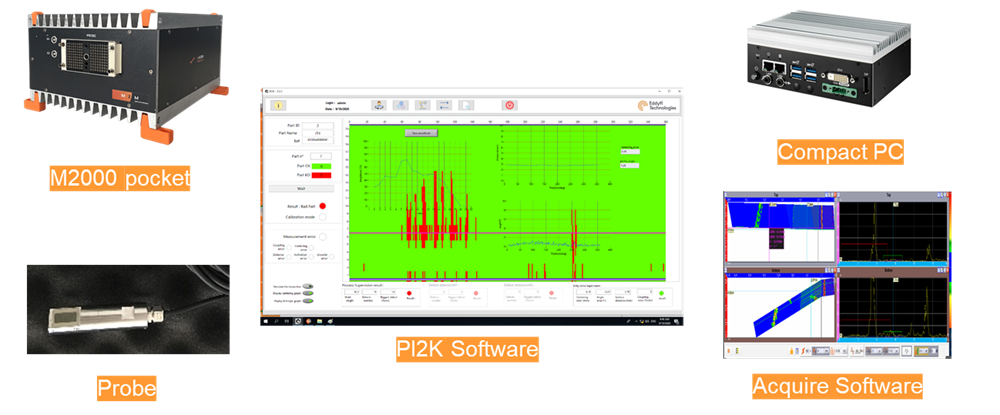
When it comes to better and faster axisymmetric welded part inspection, Eddyfi Technologies is committed to keeping you Beyond Current with our advanced solutions that are adaptable to your current quality assurance processes. See where else our technology is making a difference for automotive manufacturers here, and contact us to discuss your specific requirements with our friendly and knowledgeable experts today!
Authors: Frédéric Reverdy & Eric Boujon