Real-World Reliability, Modeled for Demonstration
When it comes to testing the essential components that comprise a space bound vehicle, volumetric NDT in the form of Ultrasonic Testing (UT) has been widely accepted and employed right from the manufacturing stage through to the Maintenance, Repair and Overhaul (MRO) lifecycle for spacecraft. Conventional UT data collected during ground tests enable inspectors to find and measure defects... but we're far from conventional.
Cypher® combines PAUT and Total Focusing Method (TFM) capabilities in one intuitive platform, enabling faster, more accurate inspections that reveal the smallest of flaws in complex materials.
- PAUT allows inspectors to steer and focus the ultrasonic beam without moving the probe
- TFM synthetically focuses energy at every point within the region of interest, providing full matrix capture and unmatched resolution
Simulated Rocket, Real Technique Sensitivity
In the following video, you can see a cross section of the rocket as we move down to the boosters in the 3D crystal model. This example of TFM illustrating the shape of the rocket with laser impacts measuring 0.1 millimeters (0.004 inches) demonstrates the technique sensitivity, making it an excellent candidate for High Temperature Hydrogen Attack (HTHA) and other real-world applications. Learn more about Detecting HTHA Before It’s Too Late in our application note.
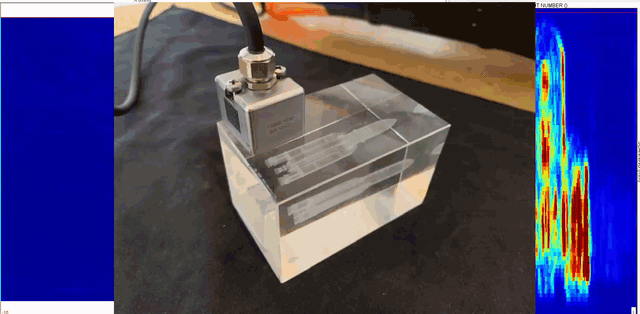
Portable Power for Real Launch Vehicles
Cypher pairs with semi-automated and automated ultrasonic testing (AUT) scanners for quick mapping of large plates and extensive composite spacecraft infrastructure without needing to perform raster scans. Given its portable nature, Cypher is well suited for in-service MRO inspections for defects such as moisture ingress, fiber and matrix interface failure, delamination, cracking, bond failure, and buckling or fracture of fibers in Carbon Fiber Reinforced Plastic (CFRP), Glass Fiber Reinforced Plastic (GRFP), honeycomb cores and carbon laminates common to launch vehicles like rocket ships. Check out the following video demonstrating the remote piloting functionality.
A Lab Alternative for Production Use
A desktop alternative for production and industrial applications, the Panther™ 2 offers unparalleled performance and speed, leveraging advanced PAUT and TFM imaging techniques for detecting and characterizing defects formed during the manufacturing process. See a similar application with the Surface Adapting Ultrasound, or SAUL, technique employed by an automated system for composites inspection here.
Unlock Inspection Confidence
As the aerospace sector expands into commercial and even recreational spaceflight, the demand for accurate, intuitive, and future-ready inspection tools is only growing. Whether you're building the next generation of reusable launch vehicles or maintaining existing fleets, our Beyond Current solutions ensure you're prepared. It all starts with trust in your data, and the tools that capture it. Contact us to discuss your aerospace inspection requirements today!