Traditional eddy current testing (ECT) is already widely used in the defense industry for inspecting bolt holes and fasteners in aircraft fuselage. Most inspections are performed with single element, pencil-like probes used to detect small cracks around fasteners. Compared to visual inspections such as penetrant testing or magnetic particle testing, ECT offers digital data recordings, inspections through thin coatings, and does not require the use of any consumable chemicals. However, the fact that ECT is not encoded and relies entirely on the technician’s manual scanning brings a high user dependency to the technique. It also makes post-analysis and auditing difficult because the data files don’t contain any position or geometric localization to refer to.
Eddy current array builds on the advantages of ECT by offering the same resolution and performance on the detection of small flaws but introduces single pass encoded scans that remove most of the operator dependency and facilitate data analysis. Displaying the data in the form of a comprehensive color map (C-scan) makes a world of difference when the time comes to identify crack indications. The strong capabilities of ECA for the inspection of aircraft structures have been proven time and again, with this example of longeron inspection and this one of rivet hole inspection.
Other than the inspection of rivets and fastener holes, military NDT personnel are often met with unique challenges that cannot be addressed by any technology apart from ECA. One of the best examples of this is described by the Royal Australian Air Force (RAAF) in this Australian Defense Business Review article. The RAAF’s efforts to monitor corrosion found in in-flight refueling hoses has led them to work in conjunction with Eddyfi Technologies to develop a novel ECA-based inspection solution and method. Visual inspection could not provide any information because of the hoses’ external coating, and traditional eddy current testing was unable to detect corrosion reliably because of the complex structure of the hose itself. In comparison, the ECA method allowed the detection of corrosion reliably and at an early stage of propagation, ultimately extending the lifespan of the hoses and reducing the costs associated to their repair and replacement. As stated in their article, “The introduction of this equipment has led to advancement in new applications of this technology across the Defence and civilian aviation community.”
Another example of ECA helping protect military aviation is through the inspection of jet turbines. The disks and blades of aircraft turbines have a lot in common with those of gas turbines found in the power generation industry except that they are generally smaller in scale. However, the core principles of ECA for crack detection at the surface of the blades or in the serrations at their root remain the same. Small rigid probes with an array of coils following the exact geometry of the serrations can be tailored specifically to the “dovetail” profile to ensure the detection of cracks smaller than 0.75 millimeters (0.03 inches) long by 0.38 millimeters (0.01 inches) deep anywhere on the surface. Past projects have shown that ECA remains unequalled for this type of inspection, both in terms of speed and reliability of detection.
Finally, non-destructive testing for the defense doesn’t need to have small geometries like rivet holes or blade serrations to be at risk of developing fatigue cracks or corrosion. More than one project has involved the inspection of large cylinders that needed to be controlled with non-destructive techniques for the detection of millimeter-sized cracks, both on their external and internal surfaces. With its wide 200-millimeter (8-inch) coverage, embedded encoder, and mechanical flexibility over a wide range of diameters, the Spyne™ array probe is ideal for inspecting the external surface of these cylinders within a few minutes. For the inner surface, Eddyfi Technologies’ custom product team developed the so-called ‘X-scanner’ which uses the same flexible probe as the Spyne but includes a rugged and encoded centering device that pushes the probe in close contact against the surface. Three sets of spring-loaded wheels ensure the stability and alignment of the probe during the scan. With only a few more minutes, the inner surface of the cylinders can be fully inspected with the C-scan data analyzed and the indications reported.
All these ECA solutions are compatible with the Ectane® 3, but more importantly with the Reddy® featuring powerful embedded software, a 264-millimeter (10.4-inch) LCD touchscreen, 8-hour life batteries, and overall high portability. This versatile tool opens the doors for many inspection possibilities of aircraft on military sites and beyond.
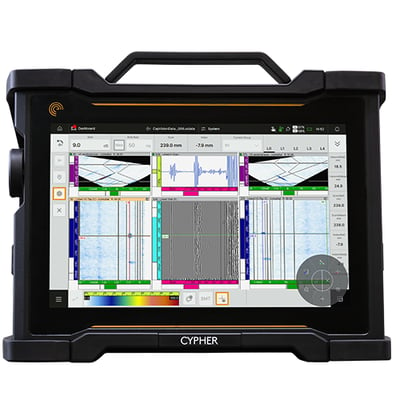
The security and defense sector play an important part in protecting public safety, and Eddyfi Technologies is committed to doing its part to provide trusted technology to help ensure the safe operation of its air, land, and sea-based assets. Have a similar application? Get in touch with our friendly experts and stay Beyond Current.